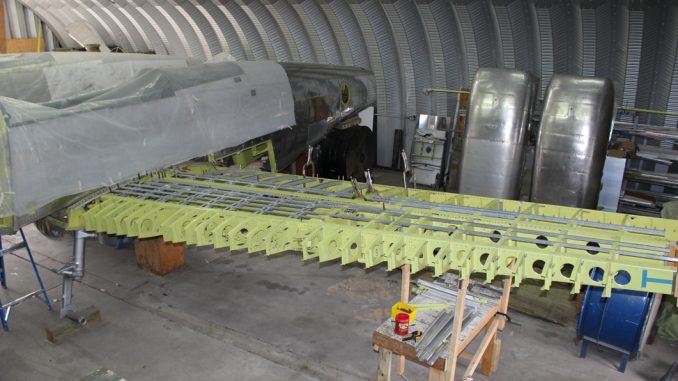
Another step closer towards the completion of the XP-82 TWIN MUSTANG #44-83887.Since January 2013 Tom and Weezie have been installing systems in the center section and both fuselages at a rapid pace.They started sub-assembling all the systems about 18 months ago, i.e., gear and retract mechanisms, electrical, quadrants, control and trim cables, trim boxes, hydraulic components and lines, stick/pedal assemblies, flap, and coolant tube systems; and then sealing them in boxes awaiting installation(s). The shelves are getting emptier and emptier every day.
Wings
The entire team–Paul, Randall, Ayman, Jeremy and Tim–have been steadily working on the two outboard wings attached to the center section prior to their going onto the steel fixture. The preliminary drill-up of the skins with #40 drill holes (tiny) on the right-hand wing is now completed. All of the fuel bay hat channels and stringers in the left-hand wing are nearing completion. By the end of January, Tom projects that both wings will be in the steel fixture for final sweep, dihedral and wash-out alignment (check the May newsletter for descriptions) and final drill-up to size and final riveting.
Control Systems
The final fitting of all the control cables and pulleys in both fuselages and center section is now completed back to the tail assembly factory breaks in the aft fuselages. The team is still waiting for three parts from the machine shop to complete the installation of the rudder pedal assemblies in the right-hand fuselage. We are now just completing the canopy opening/closing and jettison systems. As mentioned last month regarding the canopy trucks, one of the six failed NDI (non destructive inspection) due to cracks so small that one cannot see them even using a magnifying glass. One of the contract machine shops hired by Tom is now machining a replacement.
Coolant Systems & Tubes
All of the multi-layer coolant tube insulation was delivered the second week of December. A beautiful job matching the original color, texture and stitch patterns. They just completed installing all of the insulated 2” and 1.25” tubes from the firewall(s) back to just forward of where the radiators mount.
Floorboard Molds
In order to make the compound shape floorboard molds, Tom had to epoxy-glued salvageable parts from each damaged floorboard together to make a complete pair of left- and right-hand floorboards to serve as molds to be used to make four new panels. It is expected to have these two molds completed some time this coming January.
Floorboards
As critical as they have been to match everything back to as original on this XP-82 restoration–paint colors, 442 rivets, #1 cad plate, etc., etc., the team had to make a modification to the original phenolic floorboards. They have a number of original phenolic floorboards, and every one of them has fracture-failure repairs made when this aircraft was in service.
Phenolic is a laminated cotton, somewhat like fiberglass, but no where near as strong. They all had failed where the pilots had to stand on the floor panels when entering and exiting the cockpits. Tom had to come up with a non original idea, (Pat Harker actually did this mod to his F-82E), to make the floorboards out of carbon fiber with a layer of the correct color and weave cotton laminated on the exterior top and bottom of each surface giving the appearance that each panel is still phenolic. With the carbon fiber laminated in between the two exterior cotton layers, the finished floorboards will look identical to the original, but will be many times as strong.
Heat Exchangers (Oil Coolers)/Miscellaneous Parts
Martin Radiator has started on the two heat exchangers,the last needed wing jack point was delivered and is now installed.Tom is waiting the last two of five flap control arms to be delivered in January. When they arrive, the team can complete the center section to outboard wing flap tube structure and install them on the aft center section spar located under each fuselage.
This article is based on the XP-82 Restoration Project December Newsletter and it was reproduced with the permission of Tom Reilly. Visit the XP-82 Restoration Project’s website for more information.
Born in Milan, Italy, Moreno moved to the U.S. in 1999 to pursue a career as a commercial pilot. His aviation passion began early, inspired by his uncle, an F-104 Starfighter Crew Chief, and his father, a military traffic controller. Childhood adventures included camping outside military bases and watching planes at Aeroporto Linate. In 1999, he relocated to Atlanta, Georgia, to obtain his commercial pilot license, a move that became permanent. With 24 years in the U.S., he now flies full-time for a Part 91 business aviation company in Atlanta. He is actively involved with the Commemorative Air Force, the D-Day Squadron, and other aviation organizations. He enjoys life with his supportive wife and three wonderful children.
Good afternoon, very interesting restoration work, I work with restoration of aircraft damaged by accident or time here in Brazil. I would like to show you my work. This is the link to my Facebook, where I have some photos on my work. A big hug and congratulations for the work
https://www.facebook.com/macacovelho/photos_albums
Douglas, send us an email so we can talk about your work!