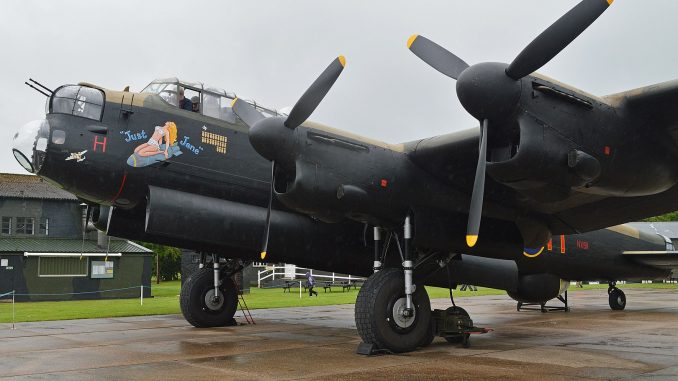
As many of our readers will be well aware, Avro Lancaster B.VII NX611 Just Jane is under restoration to airworthy condition with the Lincoln Aviation Heritage Center at former RAF East Kirkby in Lincolnshire, England. The group has made magnificent progress, even during the pandemic, and we thought that our readers might like to see a recent (edited) report, reproduced here with permission…
The Rivet Club – Newsletter 158
by Andrew Panton
We are back from our Christmas break and starting to get back into the swing of restoration work.
Thankfully we received the new wooden forming-blocks which we will use for the production of replacement aluminium formers for KB976’s rear fuselage. These wooden blocks are made in two halves, as per the aluminium formers, along with a 4″ overlap. The main forming-block is cut from 18mm plywood, with an identical shape cut from 12mm ply to clamp atop the aluminium blank sandwiched between them. This will ensure that the aluminum trapped between the two wooden blocks will not buckle whilst the edges are beaten into shape to create the new former. Under production conditions, aircraft factory workers would typically shape these new formers from aluminium alloy sheet stock in its softest tensile state, i.e. T-0, and then harden the fully-shaped part via solution heat treatment to raise its tensile state to T-3 classification. Production via this technique allows aluminum shapes to be formed with tighter bend radii, since higher tensile strength aluminum, while stronger, is less flexible and can crack if bent too sharply or over-worked. It is also a lot easier to shape aluminum sheet in its softer state as well, but there are obstacles as well, including added expenses from heat treating, time delays and then coping with the potential for adverse deformation during the heat treating process. T-3 aluminum sheet can still be shaped provided all bend radii are larger than the material limits dictate, so we decided to trial-produce formers straight out of T-3 to determine its practicality. We used an offcut of T3 material and shaped it around the forming block’s tightest radius. The trial went very well and did not result in any cracking, so we ordered the appropriate T-3 material for making new formers.John has been progressing well with NX664’s wing now that it is fully secured in the jig. He began working on the wing’s underside as the new year began, focusing on the number 2 fuel tank bay. The team has started removing the strengthening plates from around the tank bay in order to assess their condition and address any corrosion issues. We will disassemble the tank bays to clean and repair the components. We will also be working on the damaged ribs between the number 2 fuel tank and the wing’s inboard edge. This cleaning down process is extraordinarily labour intensive, so we plan to move on to a soda blasting process as soon as we can.
We have managed to begin inspecting some of the parts we brought back from the Kent Battle of Britain Museum last summer. The first parts we have cleaned up are the two Hamilton Standard propeller domes. At first glance, we didn’t hold out much hope for them, and we certainly wouldn’t have bet any money on them being in good condition given their history. In a surprise to us all, and giving us the year’s first good news, both domes came apart with relative ease and proved to be in very good condition. The rubber seal in the dome mechanism often traps moisture against the dome shell, which then leads to corrosion, however that did not occur in this case; they really do appear to be in excellent shape. We will inhibit them for storage, ready for a propeller overhaul company to more formally inspect the parts for certification.
The oil coolers which we collected from the Kent Battle of Britain Museum have been with Anglia Radiators since we collected them. The company has since inspected, serviced and pressure tested these components and certified them as airworthy! This was a real result for the Centre, and brings us one step closer to completing full set of power plants for the airworthiness project. The coolant radiators we collected and dropped off with Anglia Radiators, however, will need new cores, and this will cost £18,000 per radiator. Although this is an expensive process, it will result in two spare radiators to match the spare oil coolers we now have. Our team should begin working through the first CASA/Heinkel power plant assembly (from the Kent Battle of Britain Museum’s CASA 2.111) soon and receive the second unit in due course – more news on that soon!
We have received a key component for the Frazer-Nash FN82 rear turret restoration. This is the spun aluminium disk which forms the turret’s base. The only remaining part we need for the FN82 is the cast ring which forms part of the mount and rotational mechanism for the turret. We expect another turret update soon and I will publish this when it is available.We’re a little light on news this week, but the rest of the team will arrive soon and we should see some nice progress in all areas as the team get back up to full force.
Stay safe and thanks for your support. Andrew PantonBelow is the latest video of the restoration work…
That’s all for this particular update. We hope that you have enjoyed reading it. As can be seen, a lot of work remains to be done, but the aircraft is well on the way back to flying condition. It is being done in a methodical and careful manner in order to keep the aircraft available for ground-running operations during the summer months. For those interested in helping support this important project, please click HERE
Be sure to check out their store HERE as well… There are many cool items to buy which will help get Just Jane back in the air!
Related Articles
Lancaster NX611 ‘Just Jane’ – Restoration Update 156
Lancaster NX611 ‘Just Jane’ – Restoration Update 154
Lancaster NX611 ‘Just Jane’ – Restoration Update 151
Lancaster NX611 ‘Just Jane’ – Restoration Update 149
Lancaster NX611 ‘Just Jane’ – Major Announcement
Lancaster NX611 ‘Just Jane’ – Restoration Update 147
Richard Mallory Allnutt's aviation passion ignited at the 1974 Farnborough Airshow. Raised in 1970s Britain, he was immersed in WWII aviation lore. Moving to Washington DC, he frequented the Smithsonian’s National Air & Space Museum, meeting aviation legends.
After grad school, Richard worked for Lockheed-Martin but stayed devoted to aviation, volunteering at museums and honing his photography skills. In 2013, he became the founding editor of Warbirds News, now Vintage Aviation News. With around 800 articles written, he focuses on supporting grassroots aviation groups.
Richard values the connections made in the aviation community and is proud to help grow Vintage Aviation News.
Be the first to comment
Graphic Design, Branding and Aviation Art