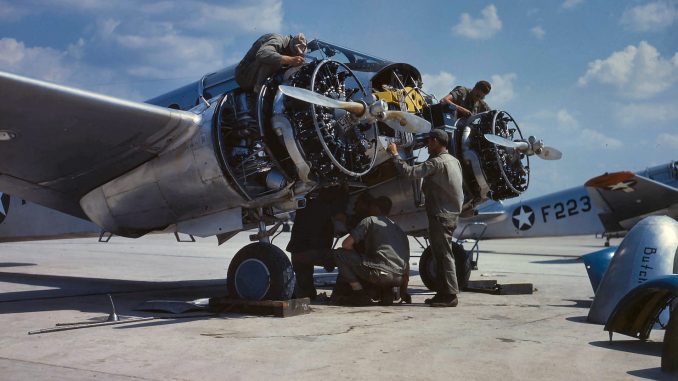
Periodically, we have presented reports from Chuck Cravens detailing the restoration of an ultra-rare Beechcraft AT-10 Wichita WWII advanced, multi-engine trainer. As mentioned in previous articles, the project belongs to the Cadet Air Corps Museum and comprises the remains of several airframes, but is primarily focused upon Wichita 41-27322. The restoration is taking place at world-renowned AirCorps Aviation in Bemidji, Minnesota, and here is their latest update on progress with the Wichita as it stands presently:
Fuselage
As the cover photo reveals, the AT-10’s nose assembly is removable, helping facilitate maintenance operations. Aaron recently fabricated and installed this Nose Assembly, Demountable, as Beechcraft described it.
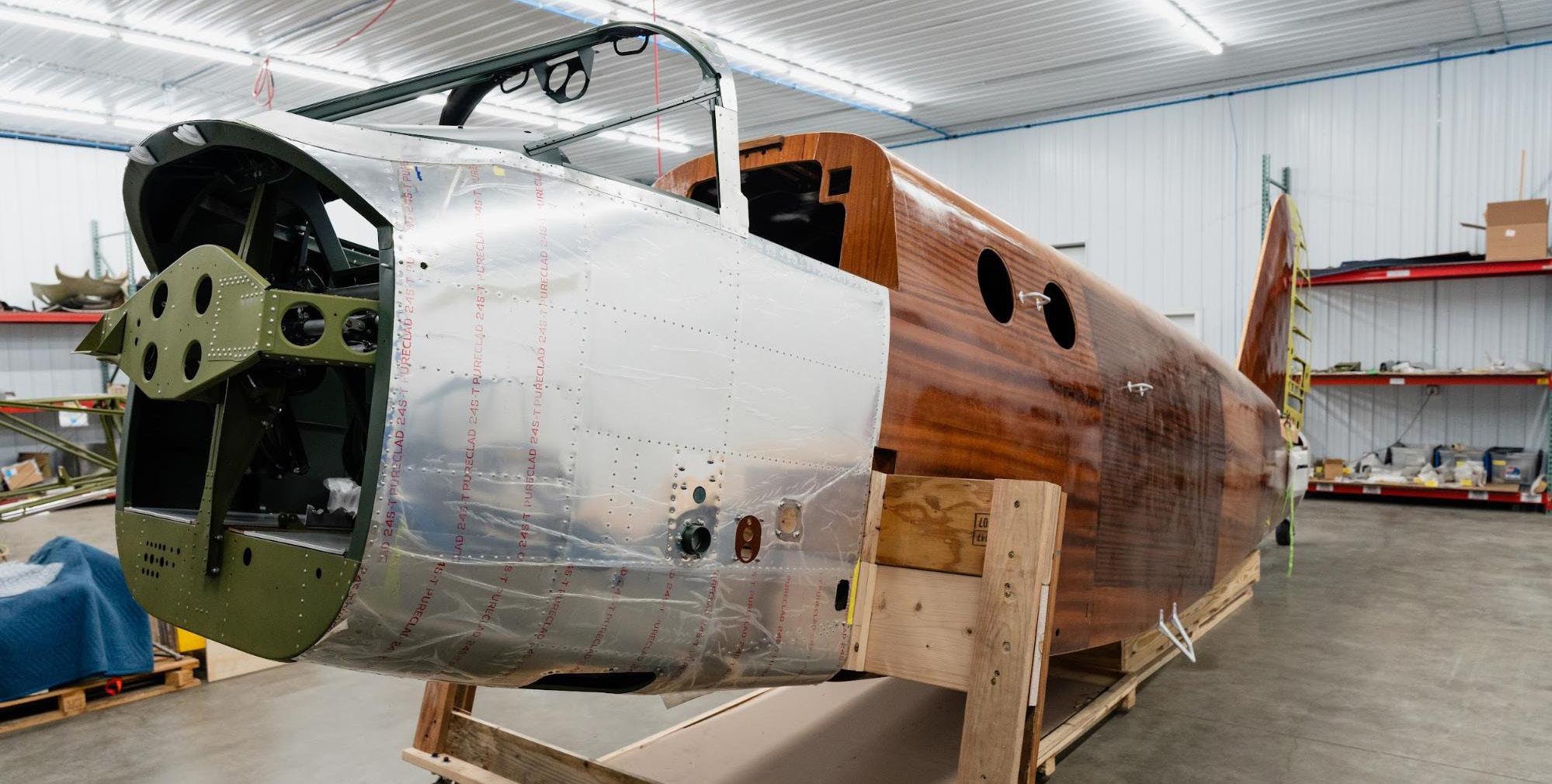
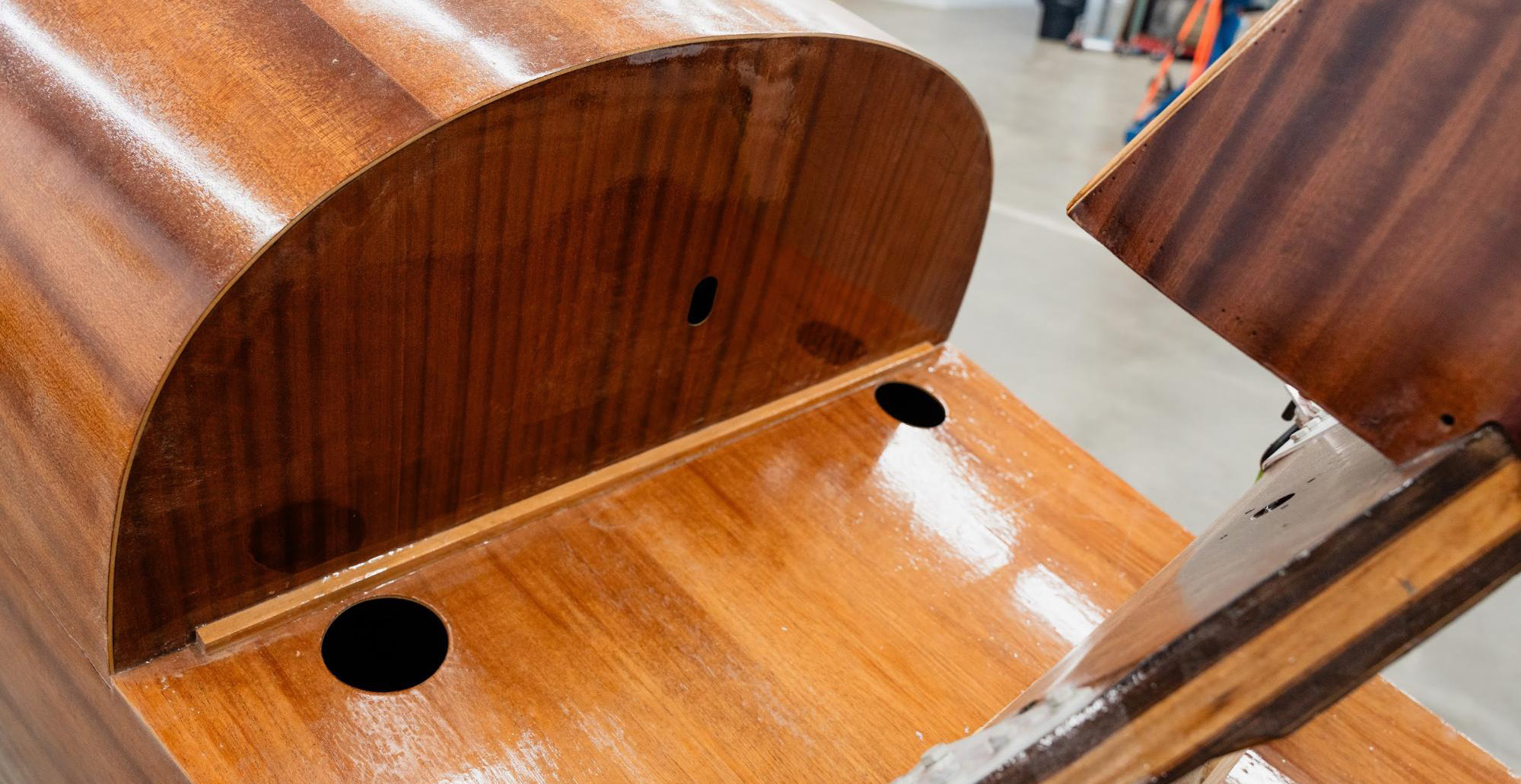
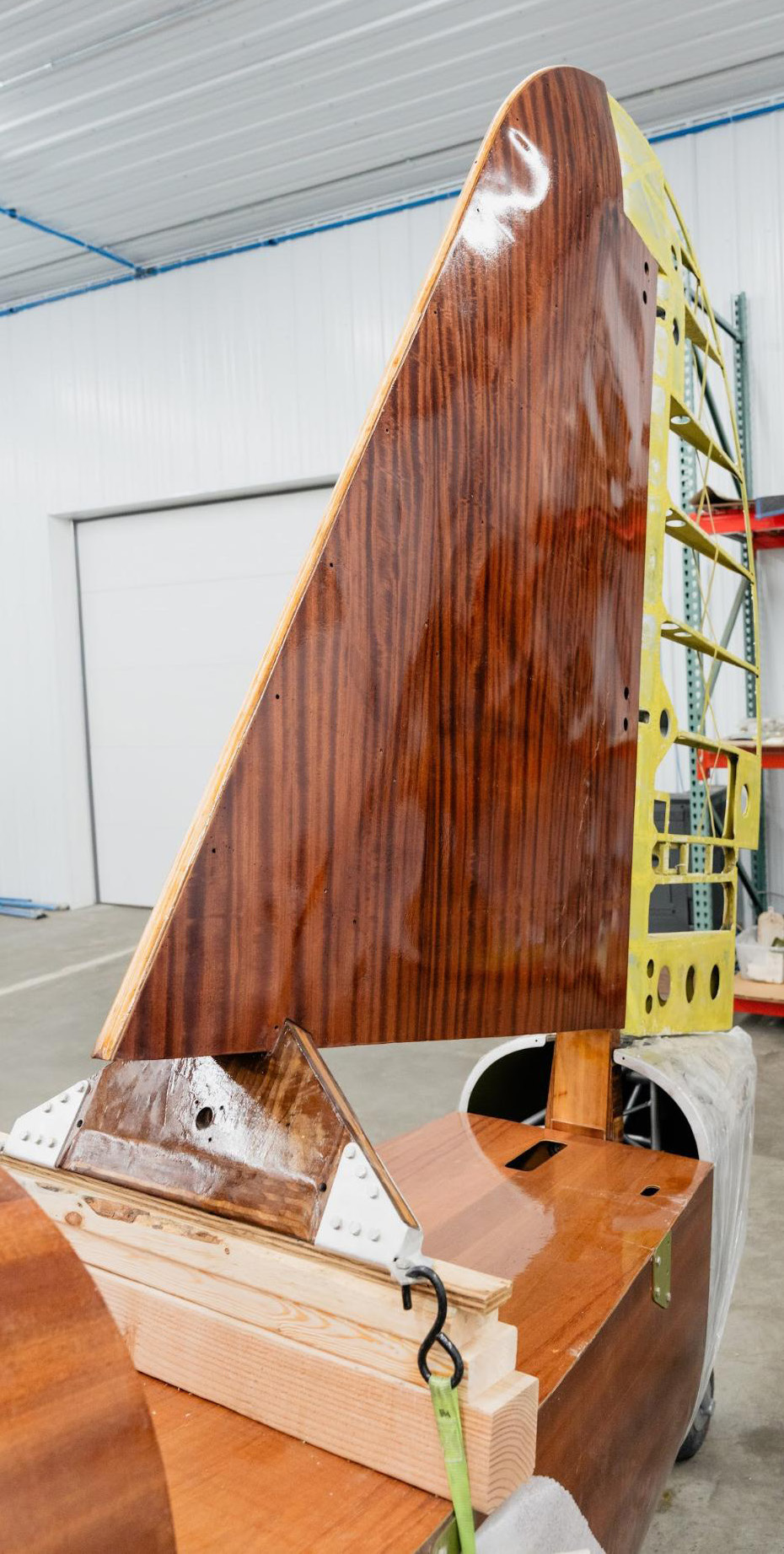
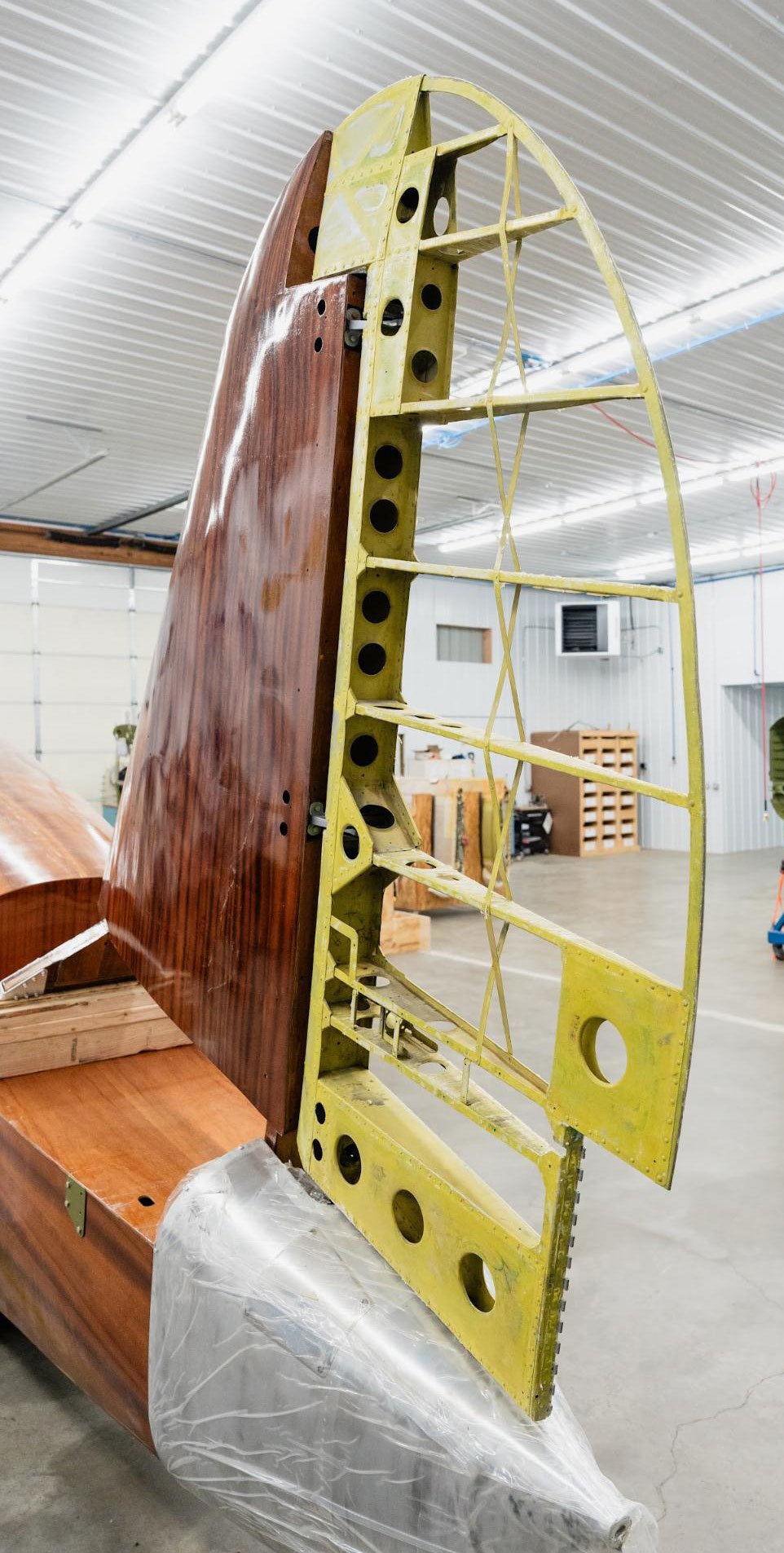
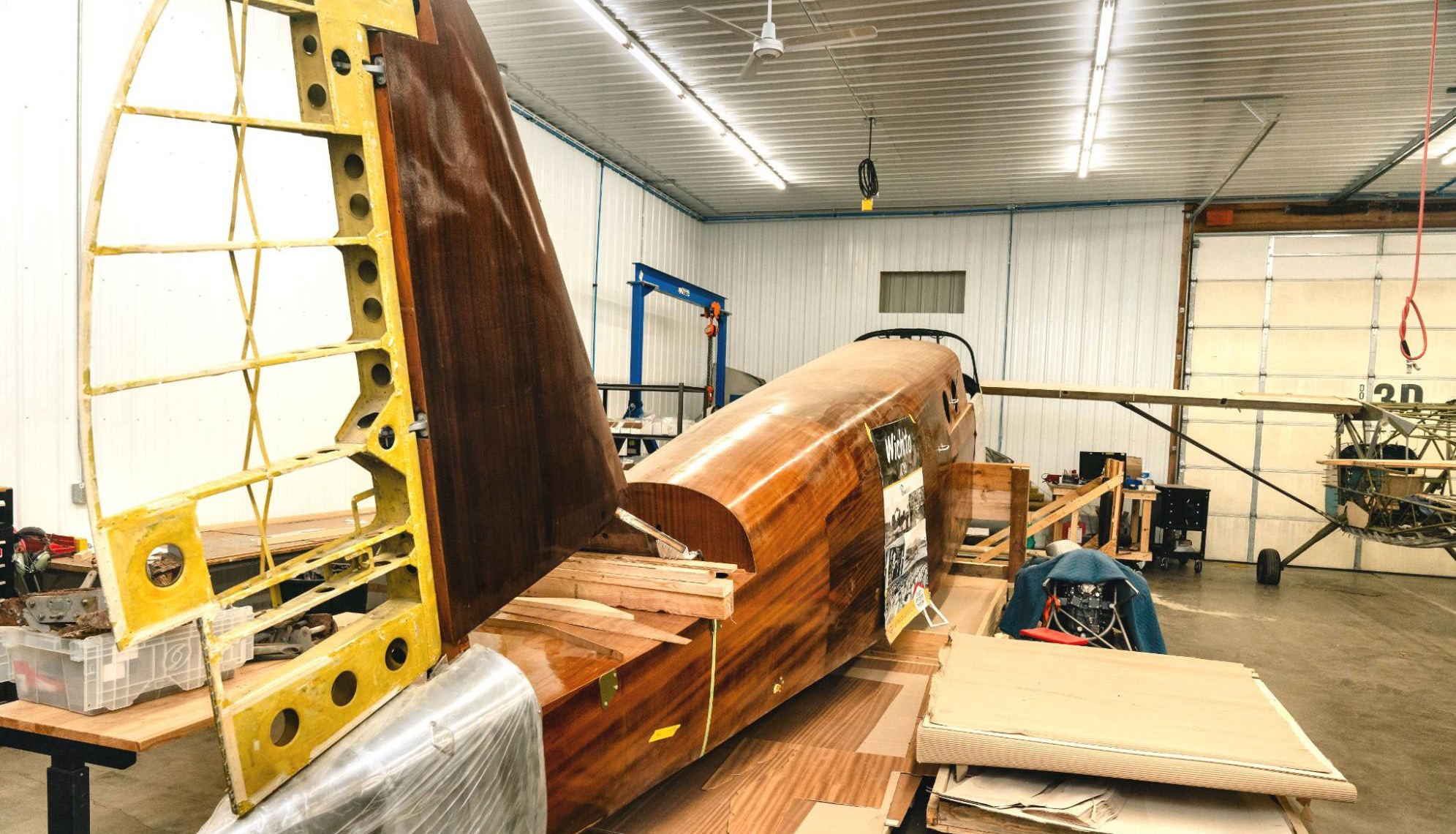
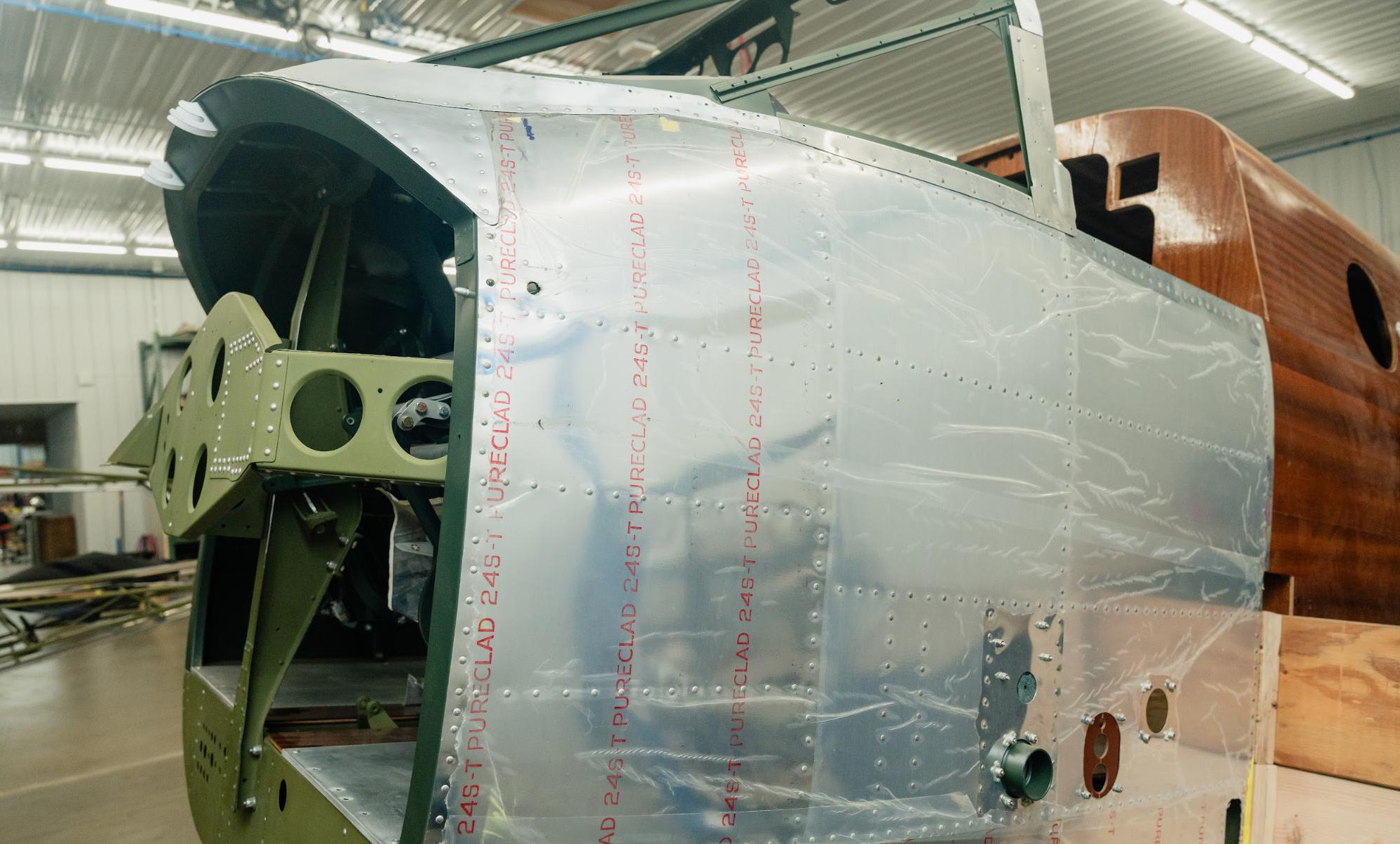

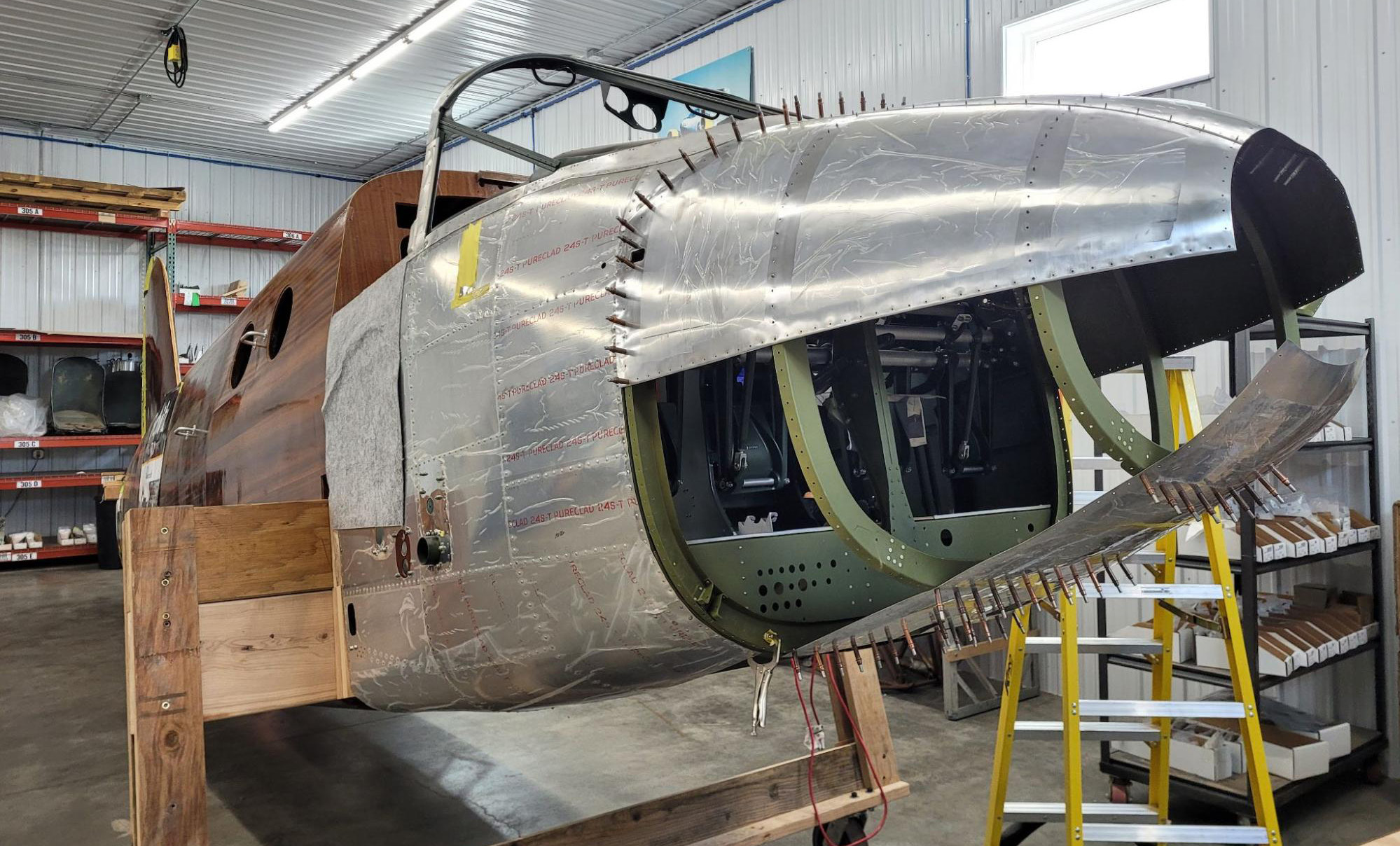
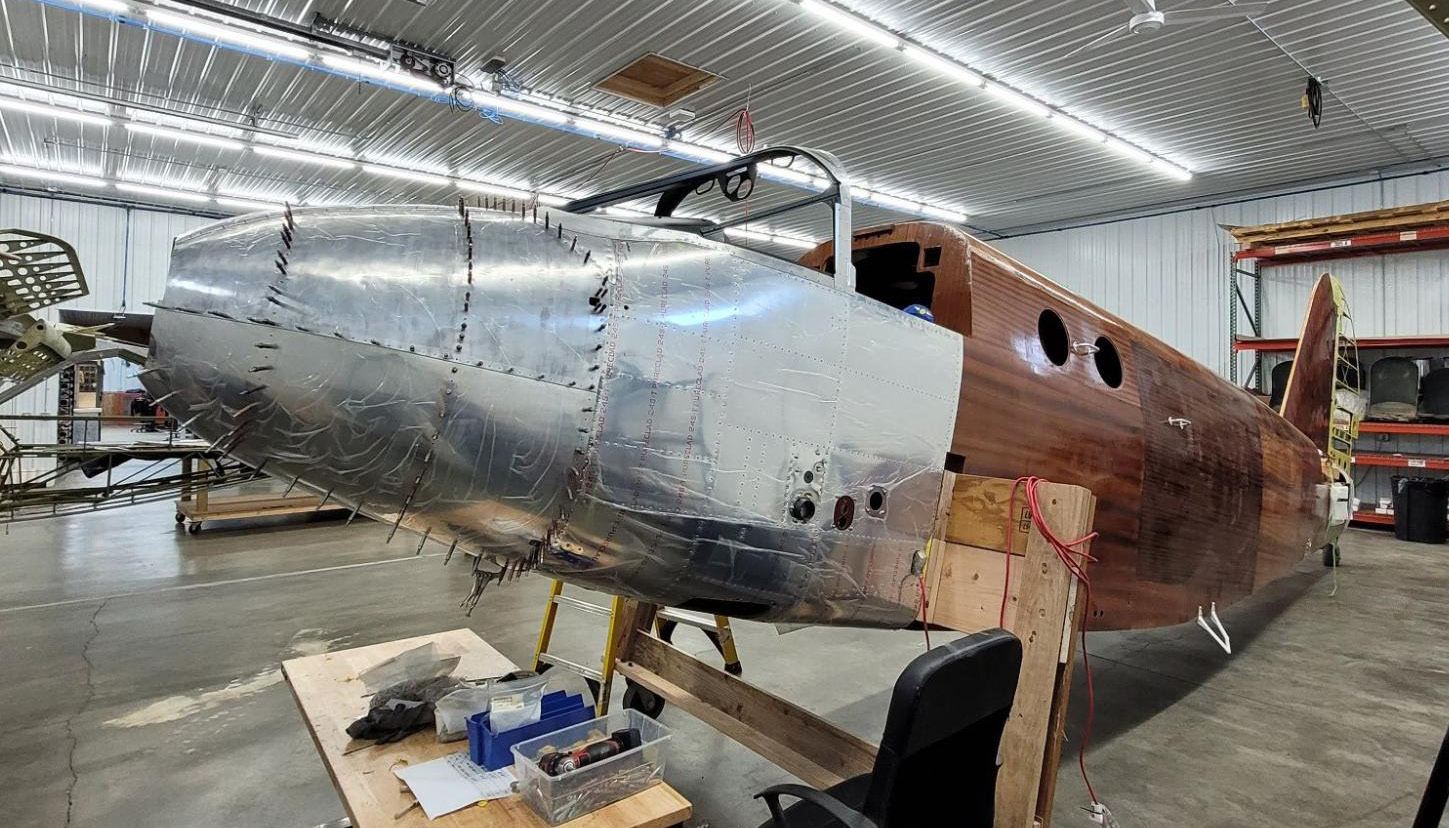
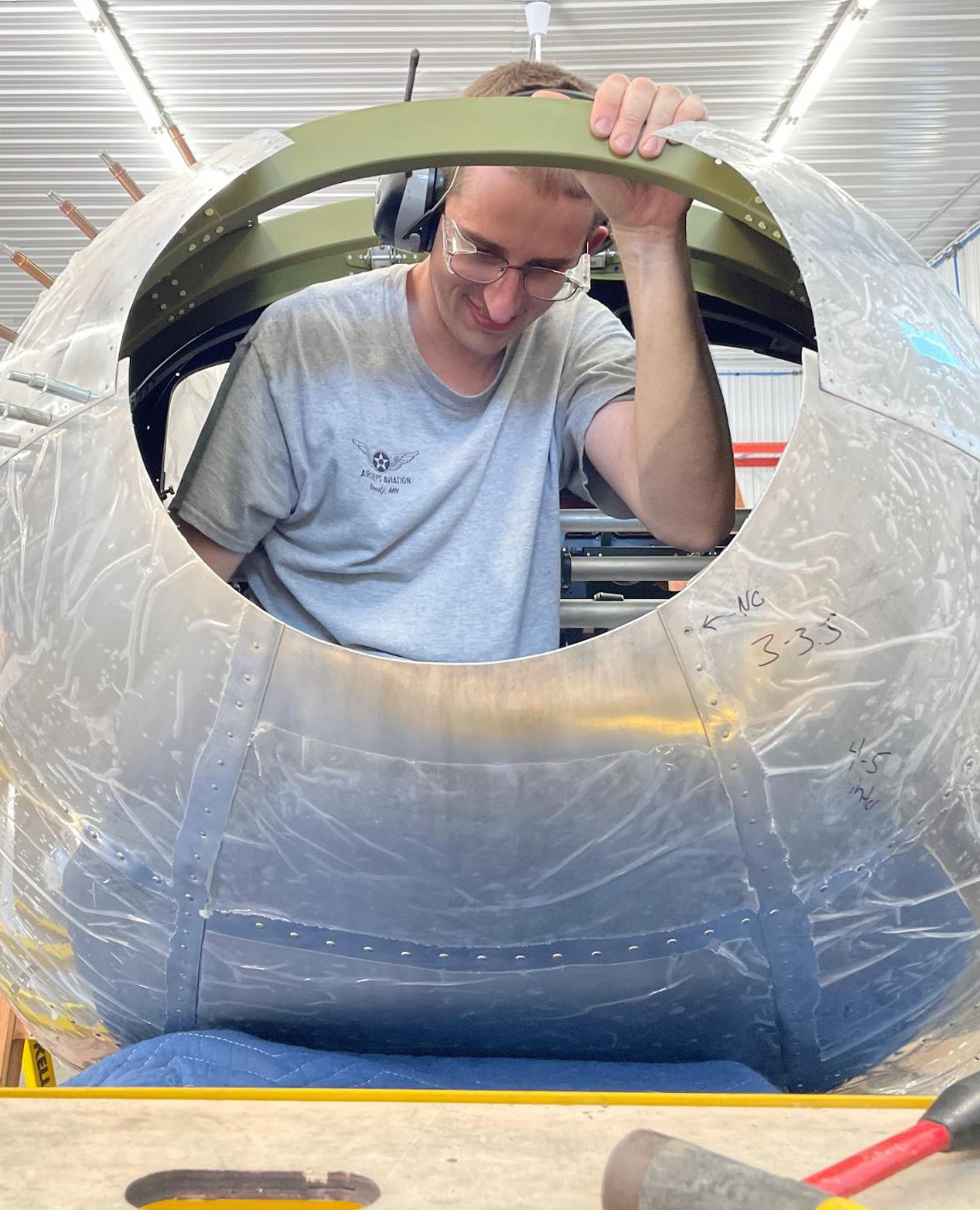
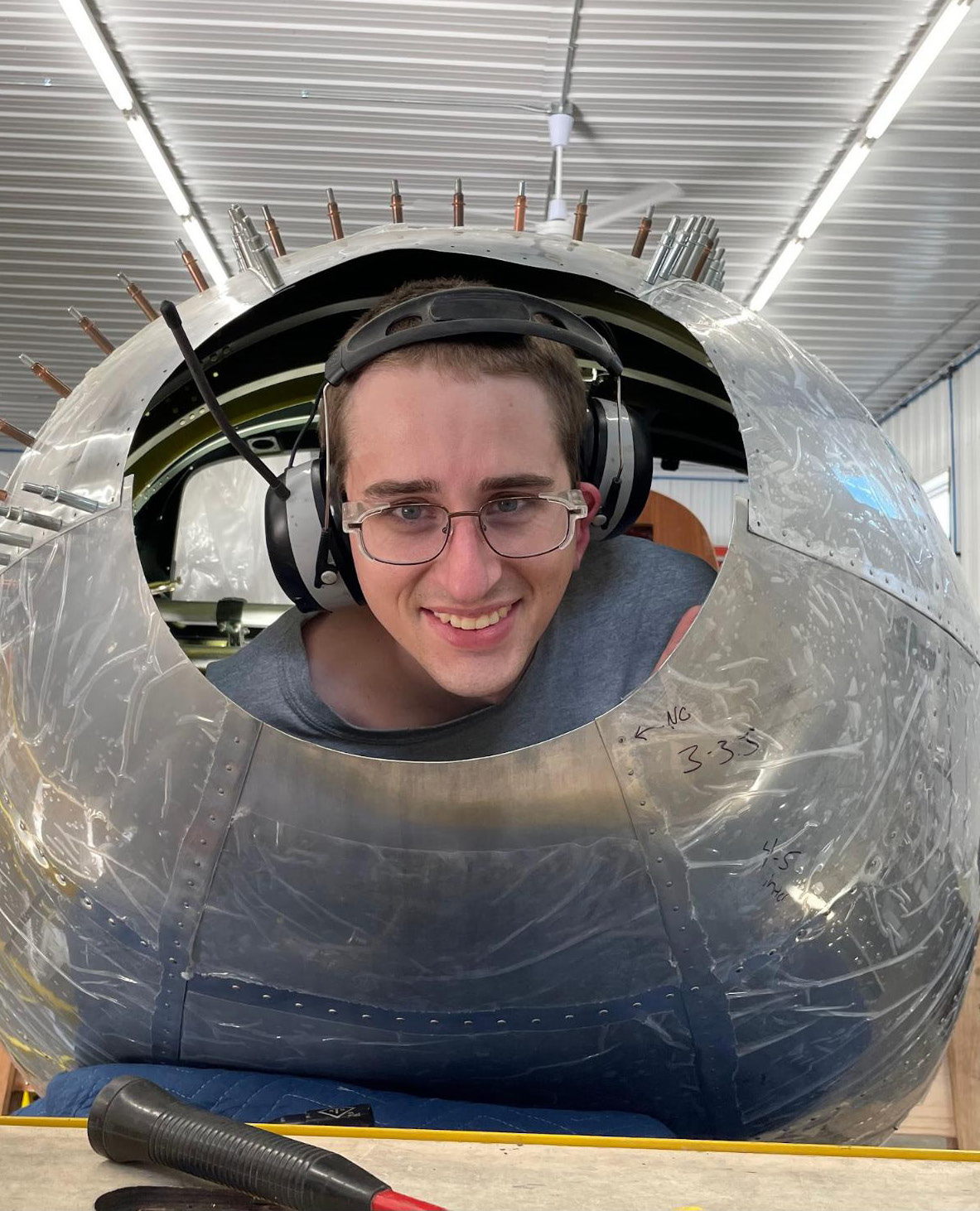
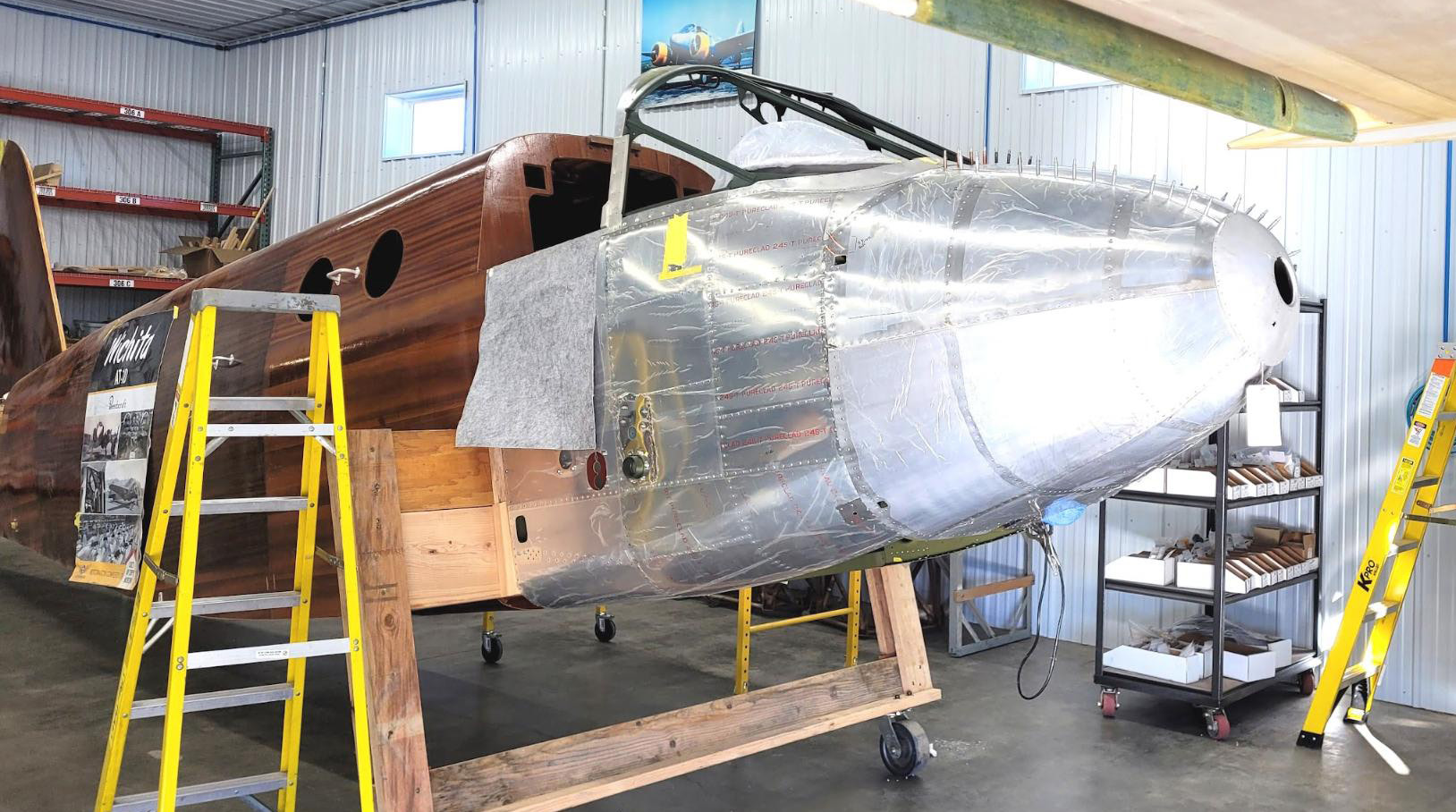
Steam Forming a Spar for the Horizontal
A mostly-wooden aircraft like the AT-10 presents a continuing challenge, with its requirements for forming and shaping wood to the required contours. These tasks can be tackled via several technicques, but the use of steam is key to most of them. The infusion of steam softens the lignins in the material, the polymers which hold its cellulose fibers together. When the wood cools, the lignins harden again, holding the material in its newly-bent condition. The horizontal stabilizer’s forward spar is one such component which requires steam-bending.
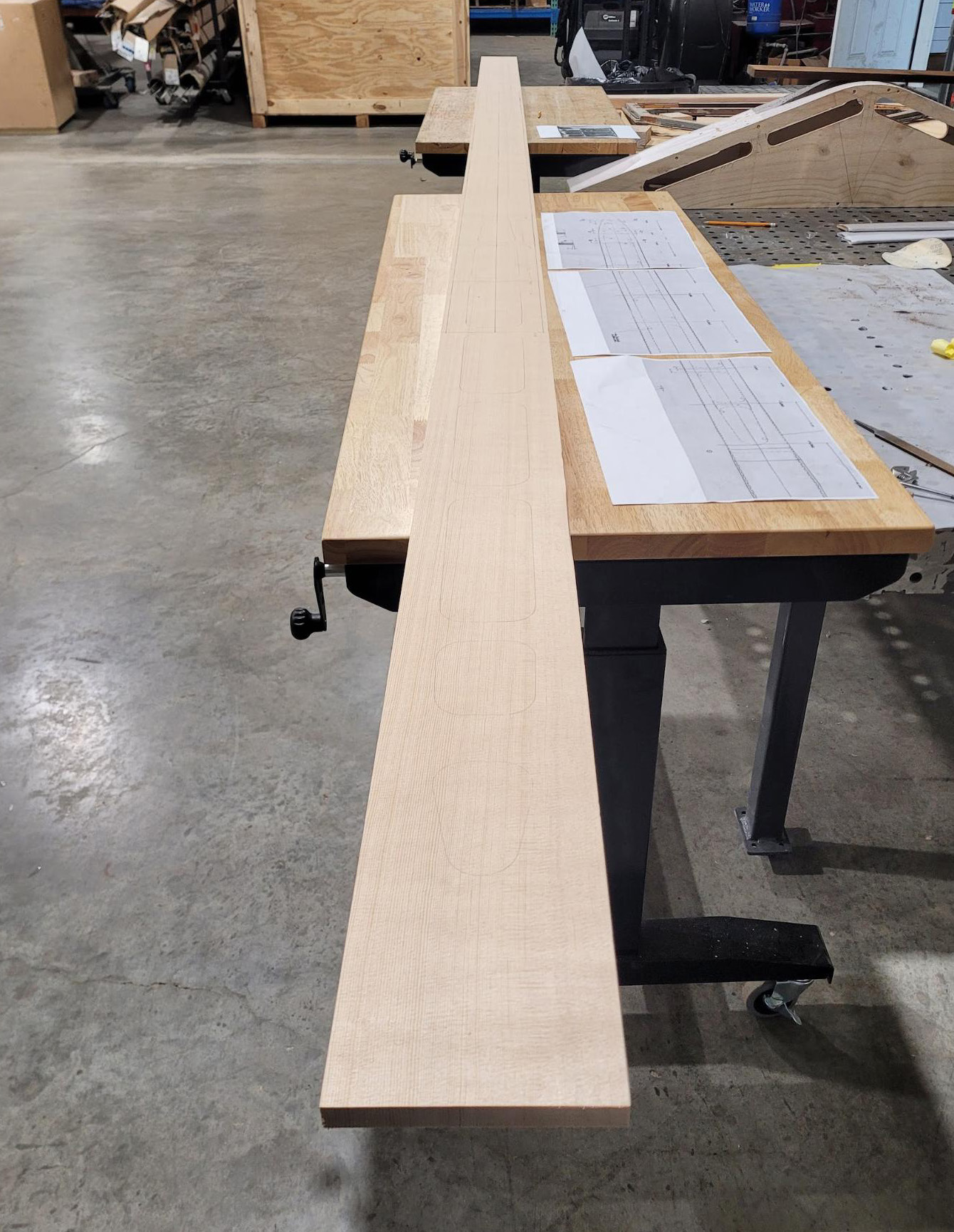
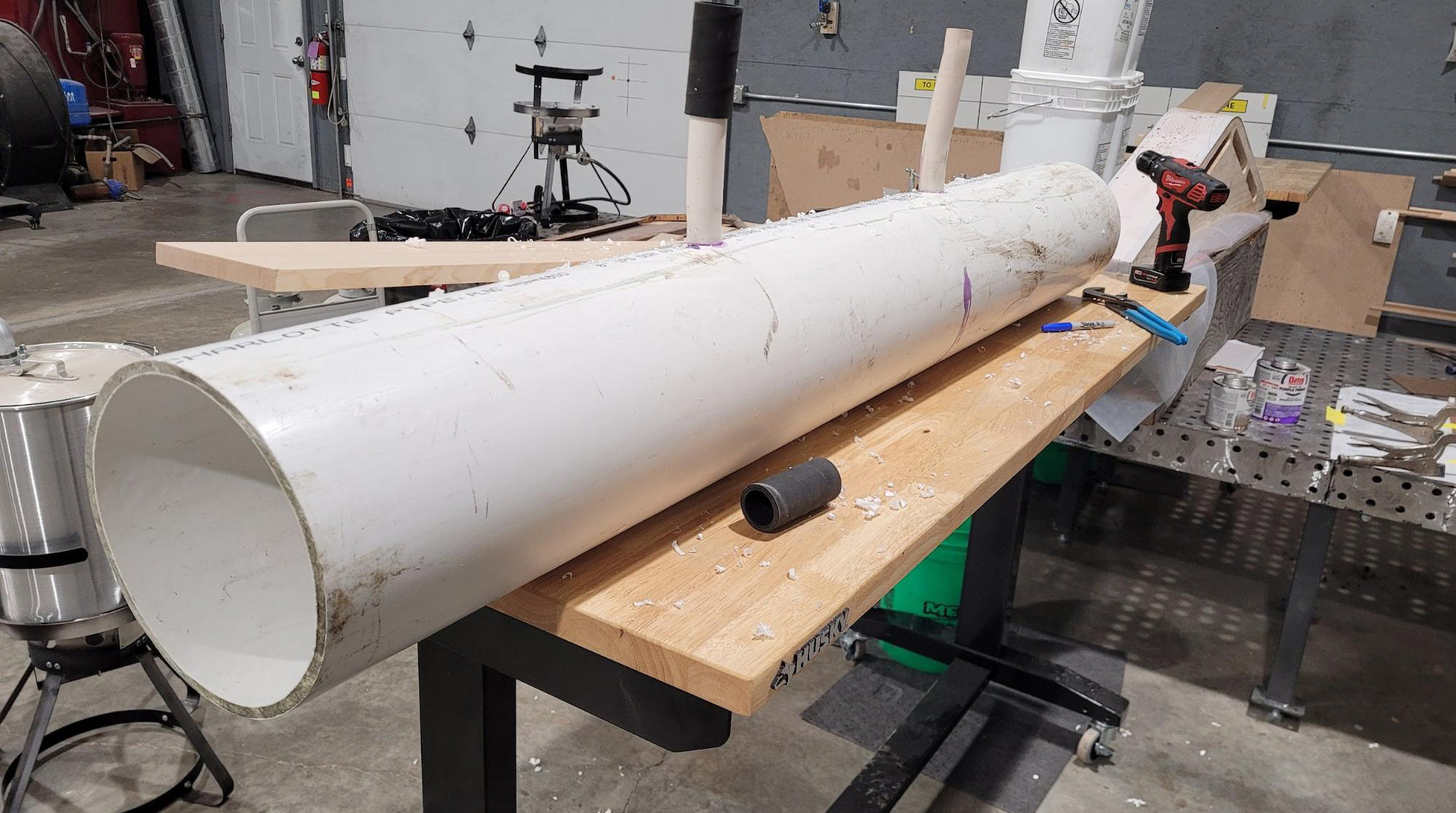
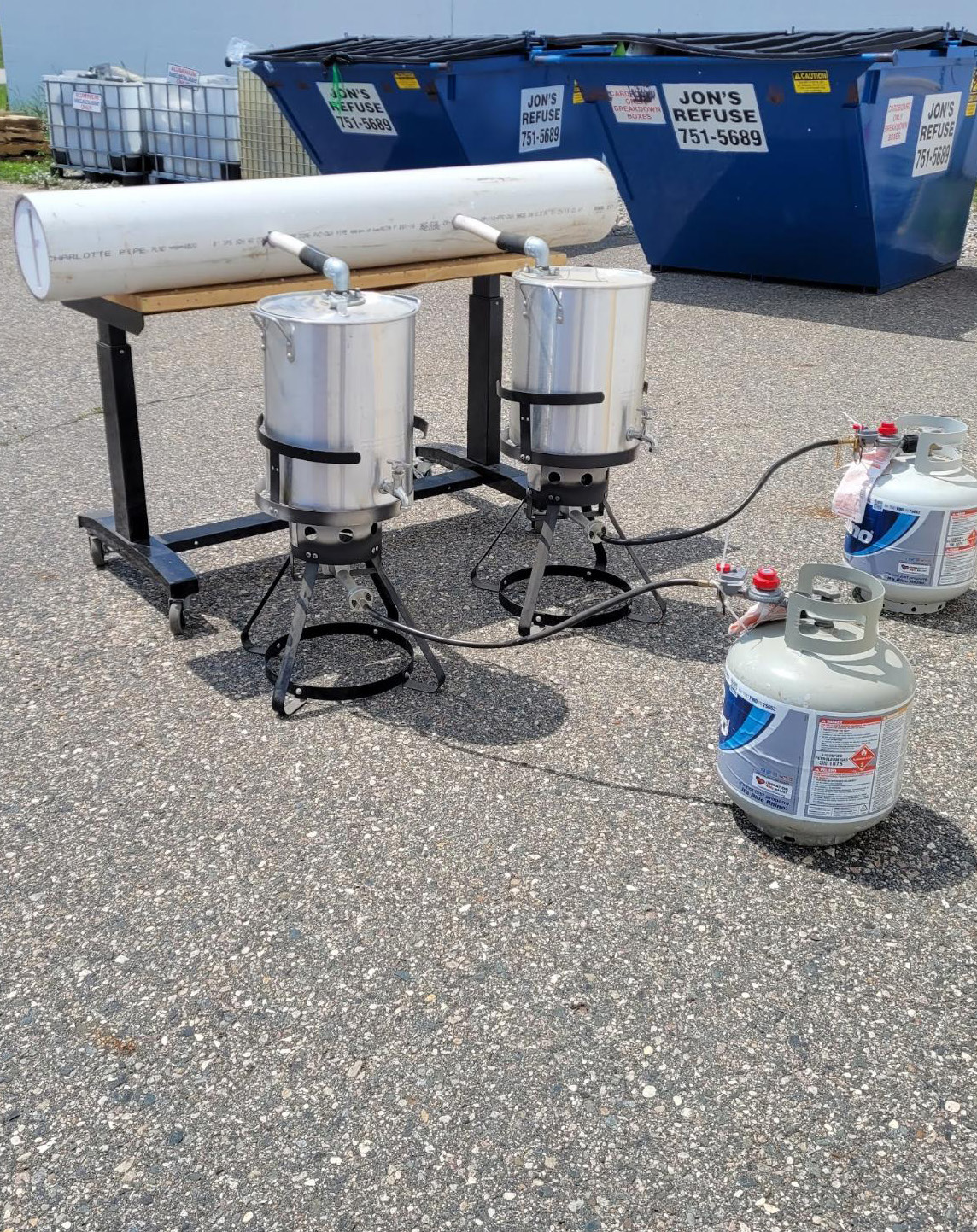
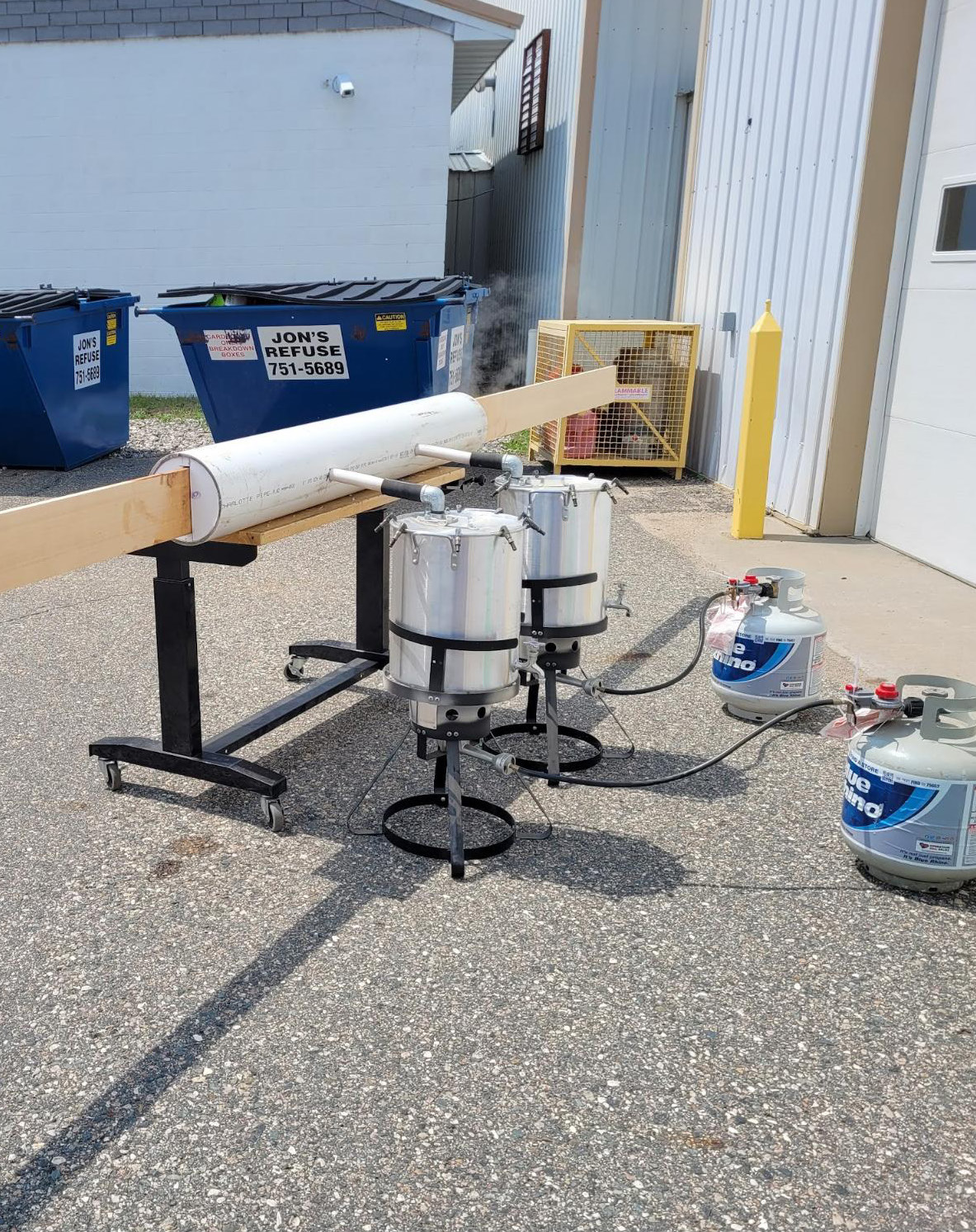
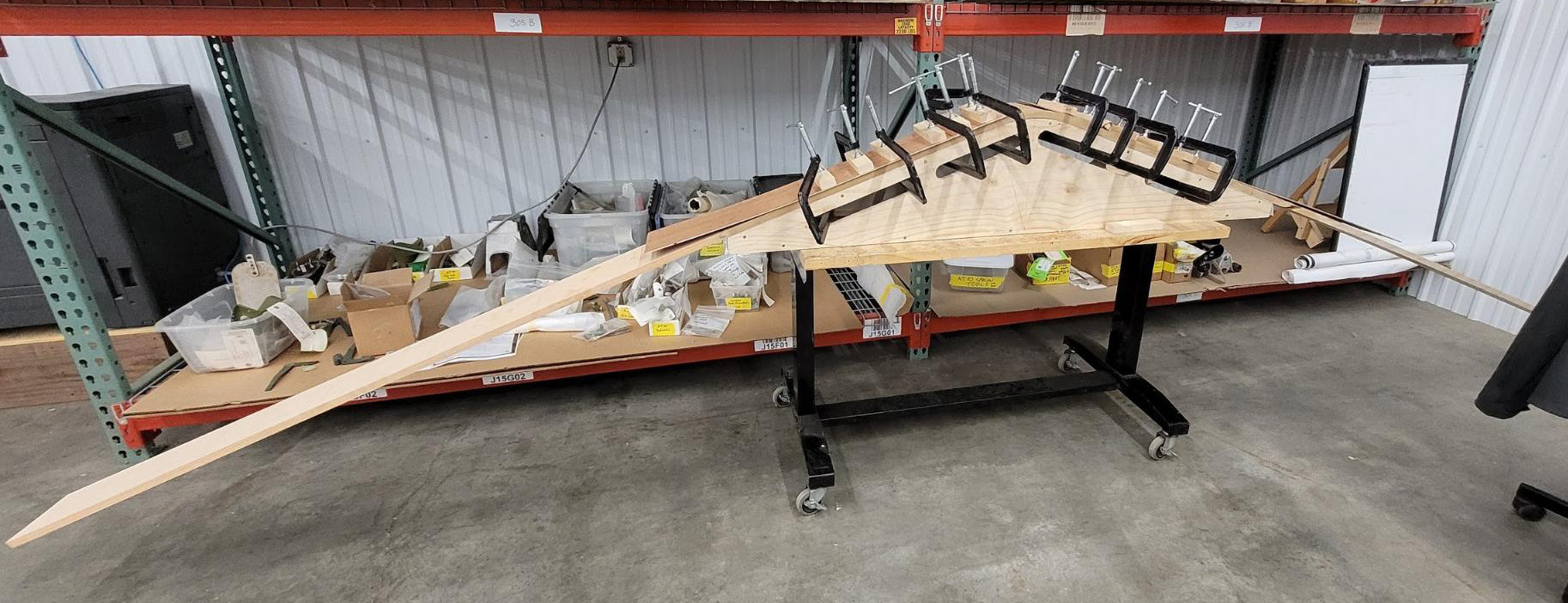
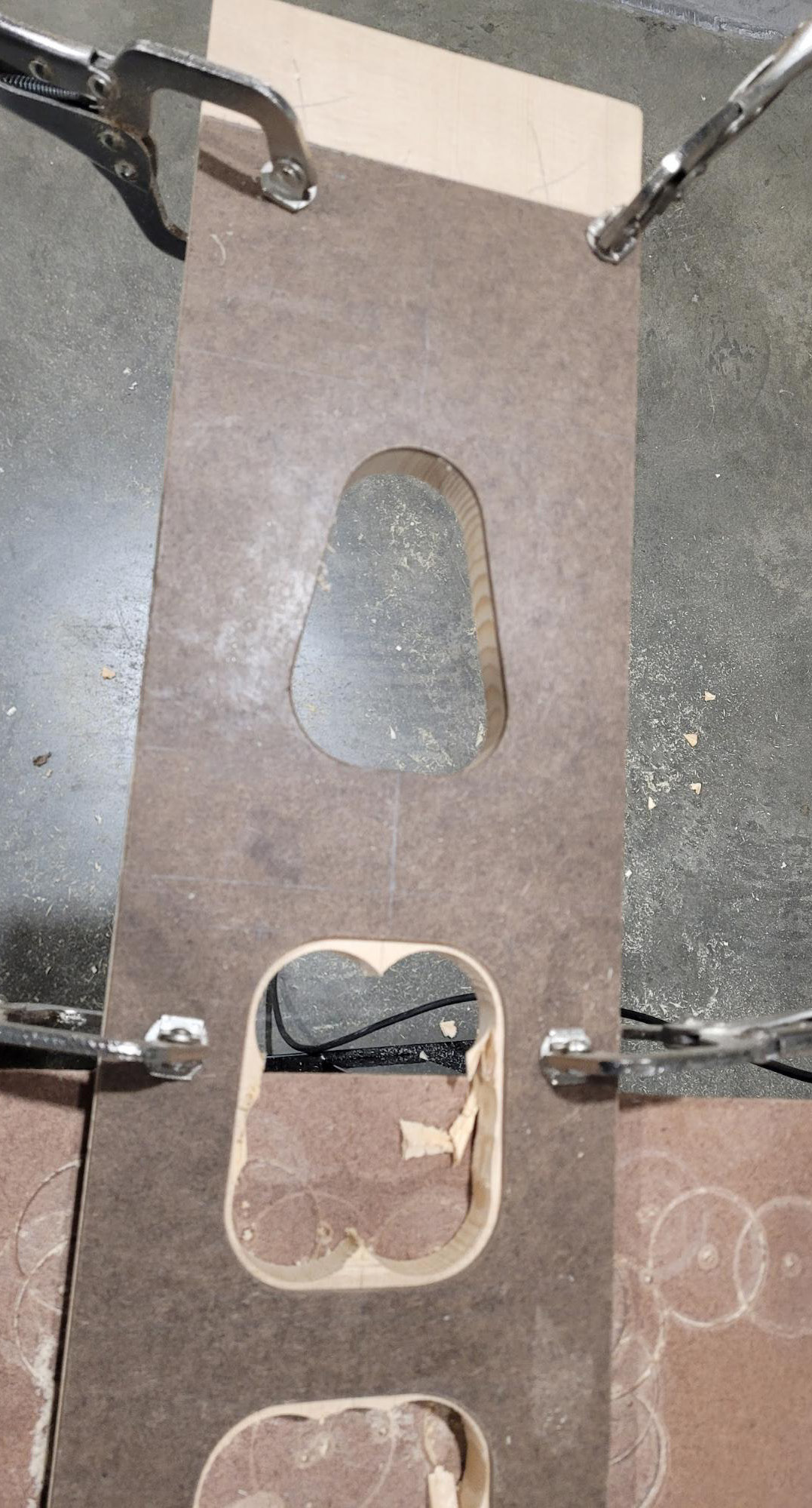
with precision. (image via AirCorps Aviation)
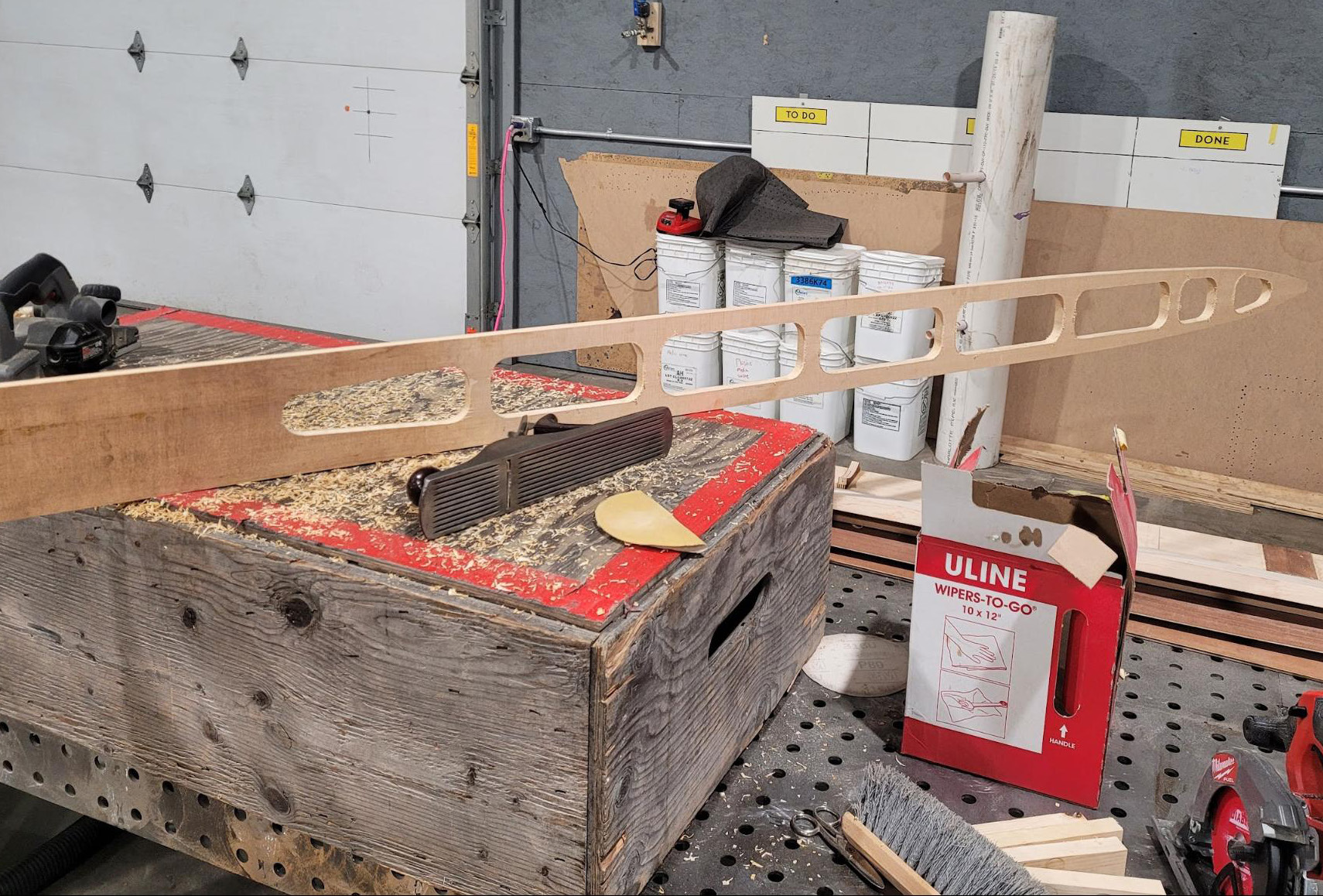
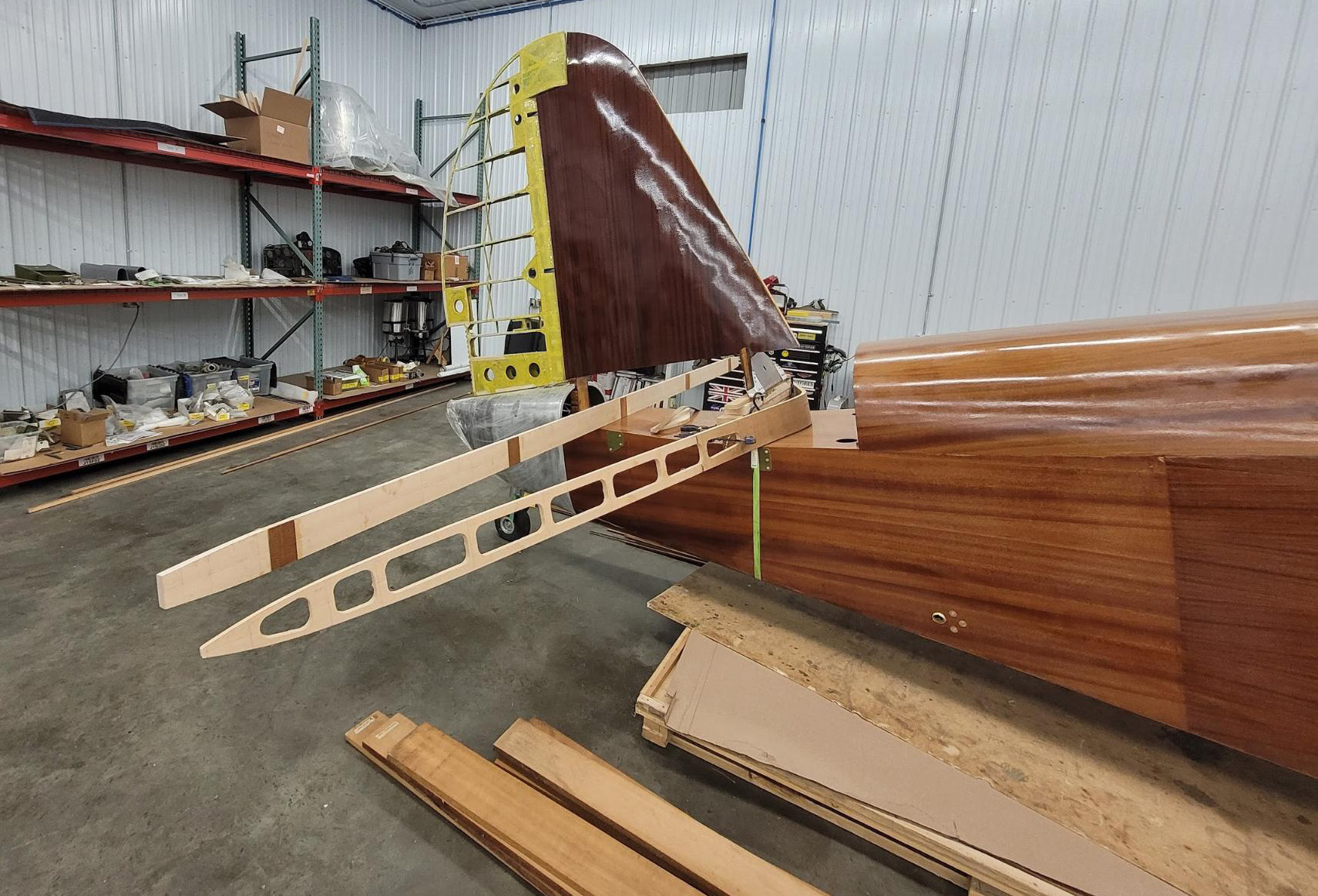
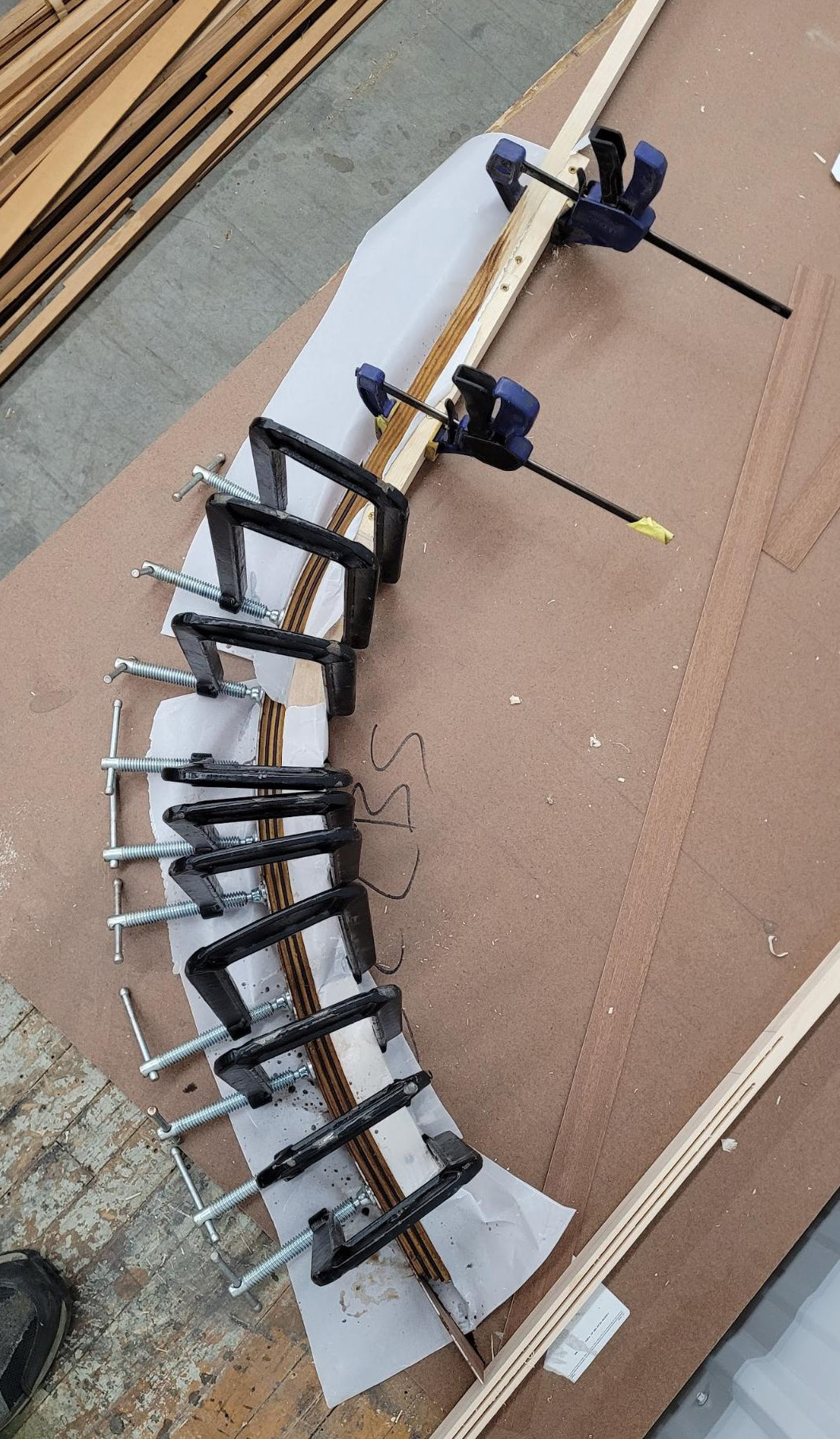
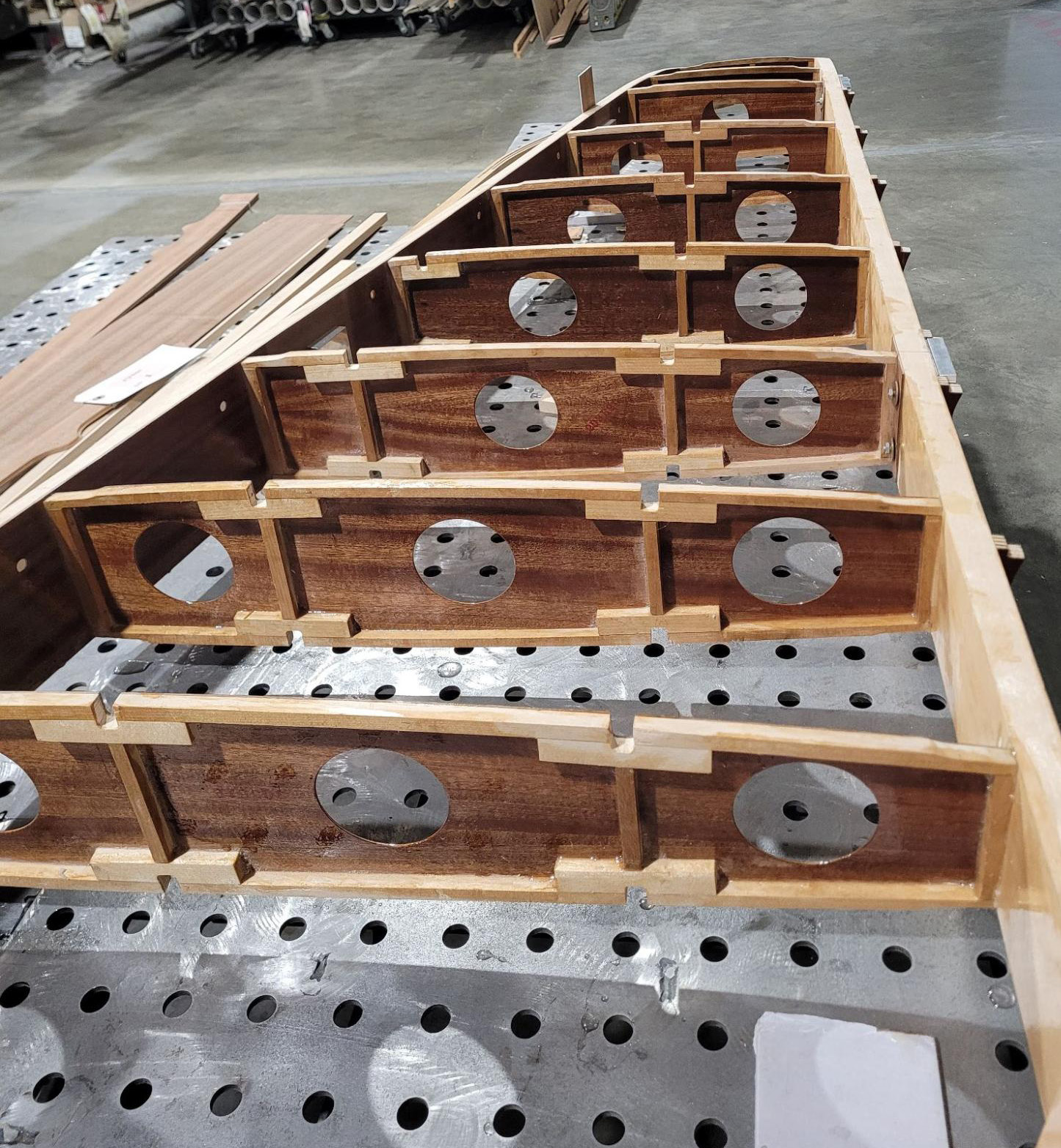
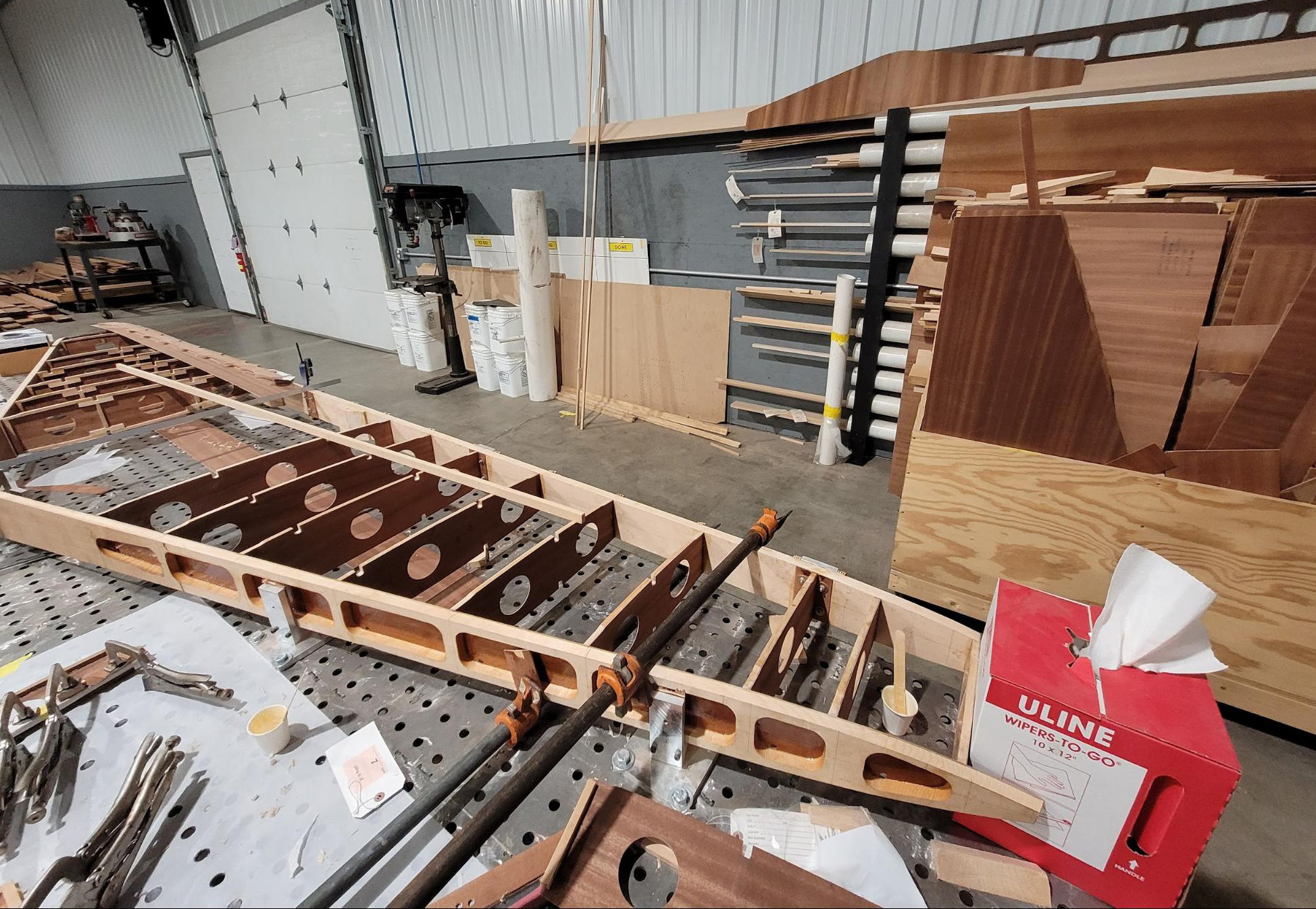
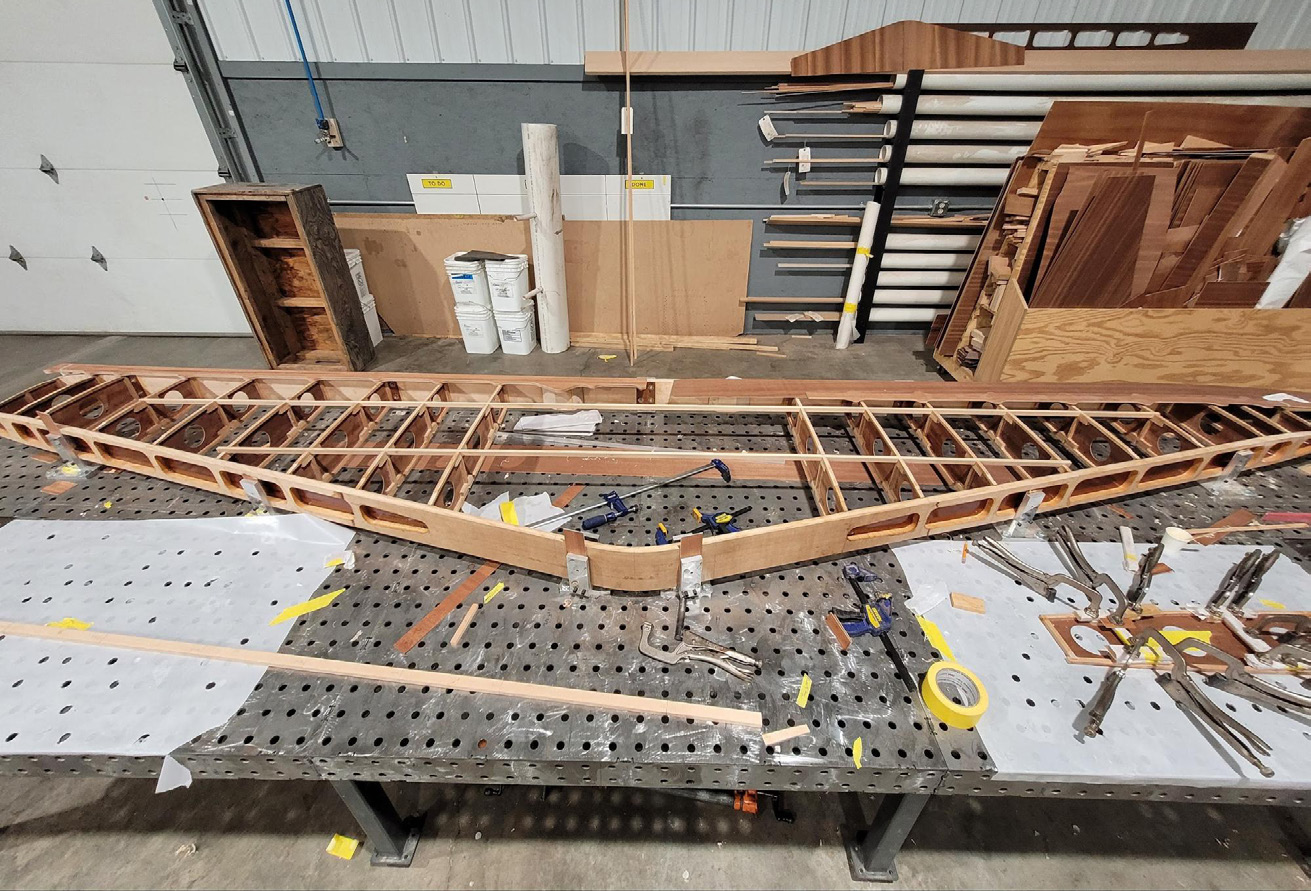
Wings and Center Section
The outer wings and center section are the next major AT-10 assemblies to undergo restoration. The work began with parts inspection, to determine which of the surviving parts we have are potentially airworthy, and which will require refabricating.
Aircraft-grade wooden materials are difficult to locate these days, with stock seemingly always on backorder. However, with their recent acquisition of Dusters and Sprayers Supply Inc. (the world’s largest inventory of Stearman parts) AirCorps Depot obtained an extensive selection of aircraft spar stock and plywood – with some 302 items now on inventory. This will be of great benefit to the AT-10’s progress, and especially its center section needs, in terms of cost, shipping, minimum order requirements, and management.
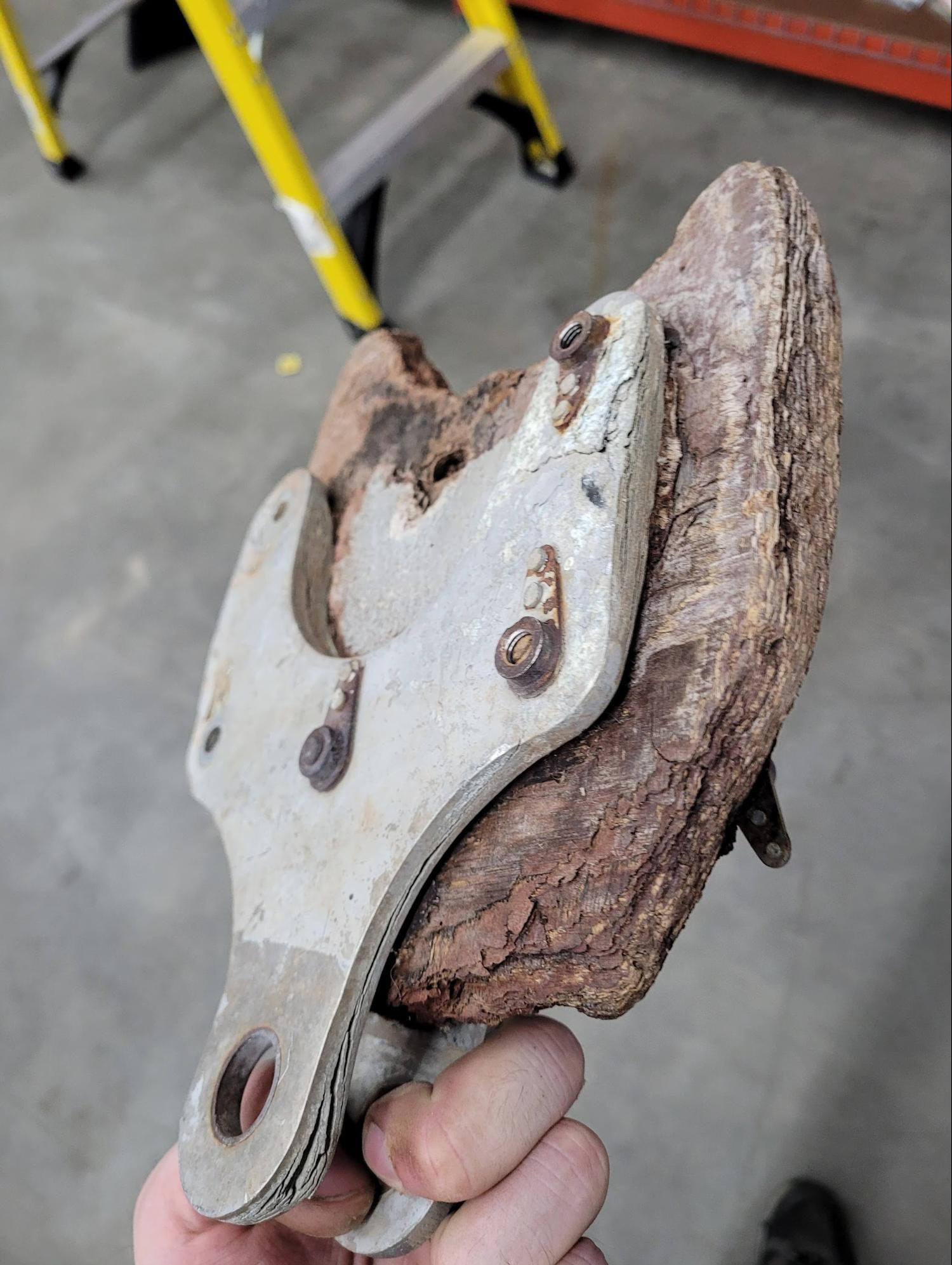
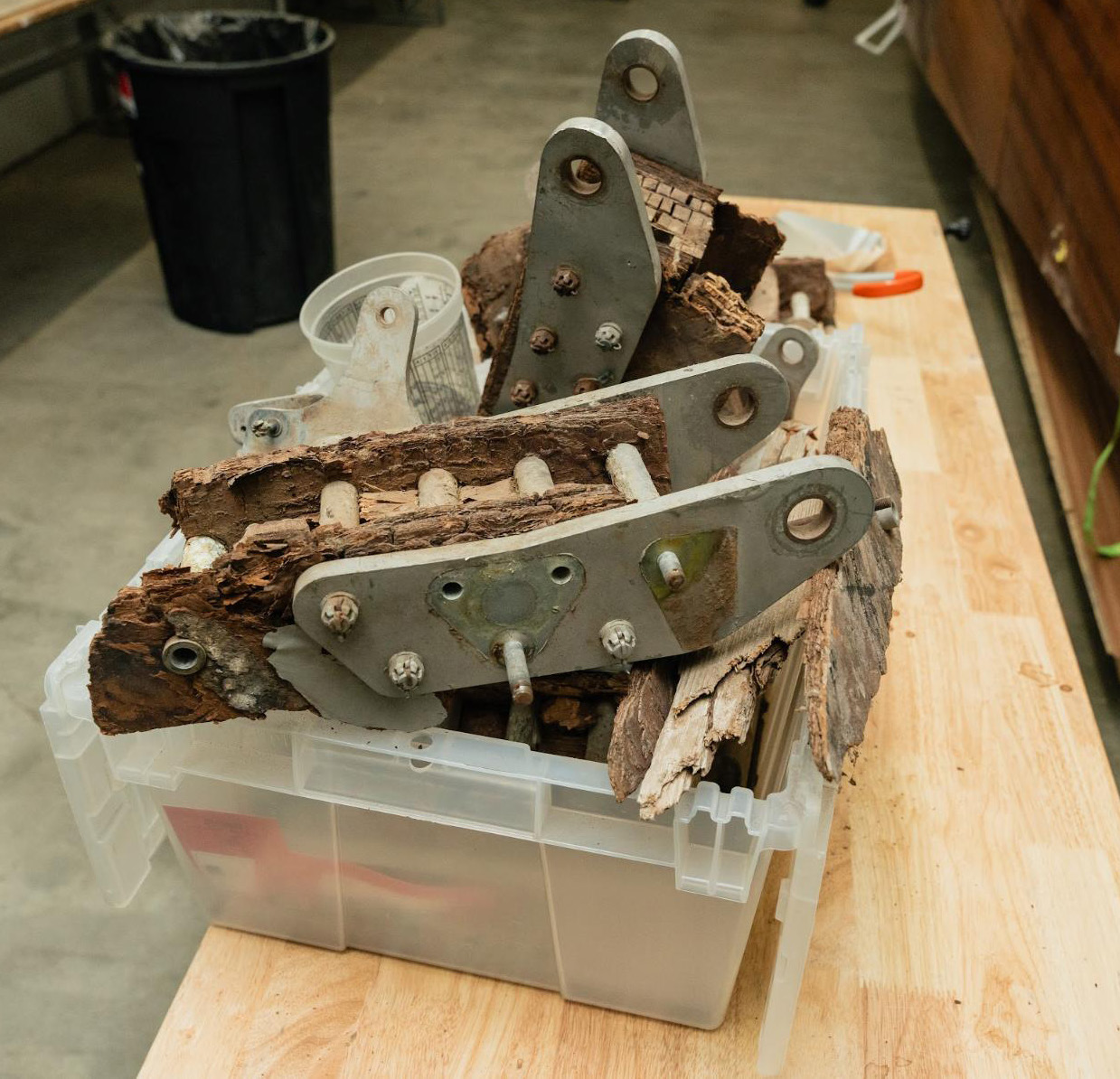
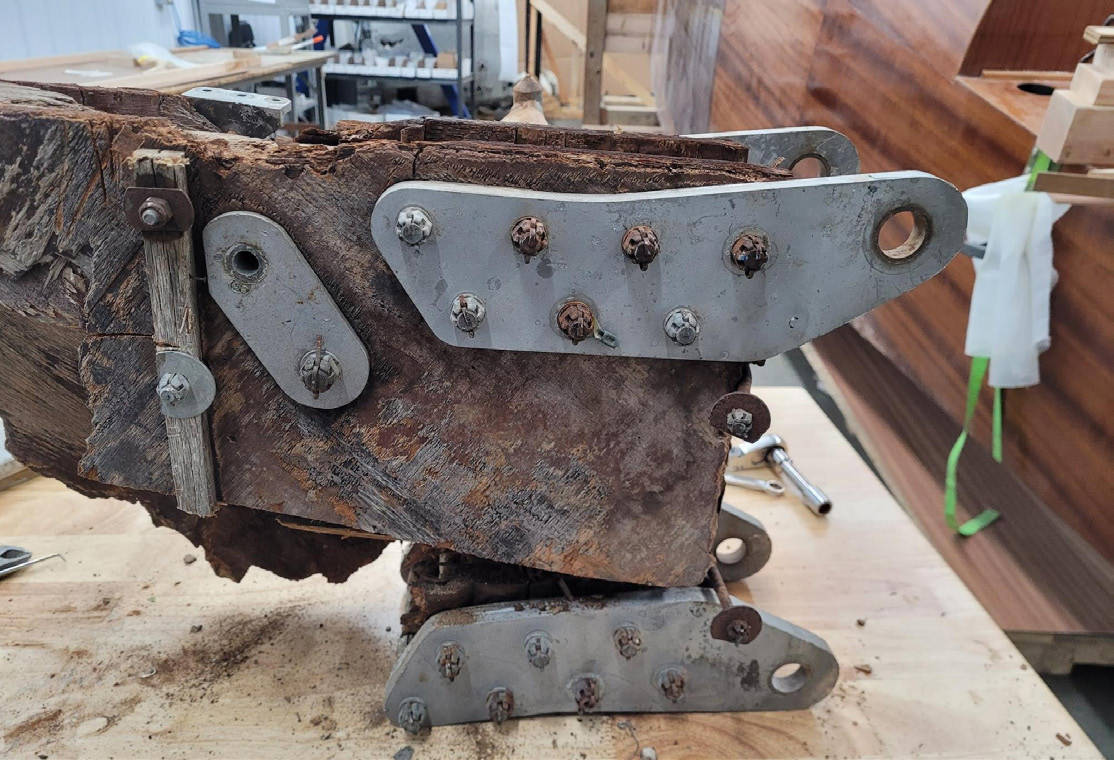
Want to get involved?
AirCorps Aviation is constantly looking for new technical material related to the AT-10. Due to the rarity of this aircraft, and the relatively low number produced, acquiring engineering drawings, parts catalogs, maintenance manuals, and other ddocumentation has been much more difficult than with our past restorations. If you have any AT-10 material or know someone who does, the team would love to hear from you!
Be a part of helping the AT-10 return to the skies! Contact Ester Aube, by email or phone [email protected] or 218-444-4478. Furthermore, should anyone wish to contribute to the Cadet Air Corps Museum’s efforts, please contact board members: Brooks Hurst: phone: +1-816-244-6927, e-mail: [email protected] Todd Graves: e-mail: [email protected]
Related Articles
Cadet Air Corps Museum AT-10 Restoration Report – Summer 2024
Cadet Air Corps Museum AT-10 Restoration Report – Spring 2024
Cadet Air Corps Museum AT-10 Restoration Report
Cadet Air Corps Museum AT-10 Restoration – Spring 2021 Report
Cadet Air Corps Museum AT-10 Restoration – Summer 2020 Report
Cadet Air Corps Museum AT-10 Restoration – Fall 2018 Report
Richard Mallory Allnutt's aviation passion ignited at the 1974 Farnborough Airshow. Raised in 1970s Britain, he was immersed in WWII aviation lore. Moving to Washington DC, he frequented the Smithsonian’s National Air & Space Museum, meeting aviation legends.
After grad school, Richard worked for Lockheed-Martin but stayed devoted to aviation, volunteering at museums and honing his photography skills. In 2013, he became the founding editor of Warbirds News, now Vintage Aviation News. With around 800 articles written, he focuses on supporting grassroots aviation groups.
Richard values the connections made in the aviation community and is proud to help grow Vintage Aviation News.
Be the first to comment
Graphic Design, Branding and Aviation Art