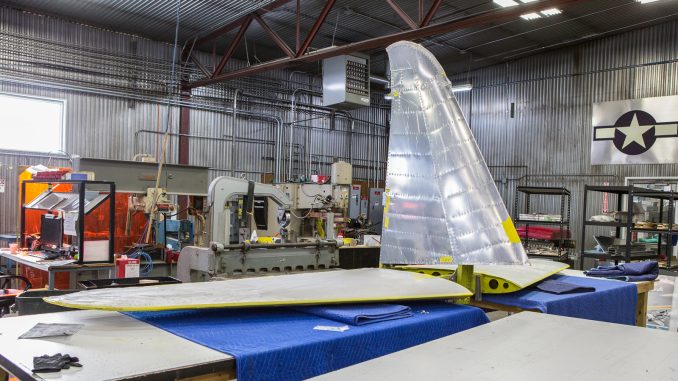
Back in September, WarbirdsNews published an article by Chuck Cravens detailing the history of Republic P-47D 42-27609. This combat-veteran Thunderbolt belongs to the Texas Flying Legends Museum, and is under restoration at AirCorps Aviation in Bemidji, Minnesota. It is a down-to-the-last-rivet rebuild, and if AirCorps Aviation’s past efforts serve as an example, which we feel sure they will, this razorback Thunderbolt will be a truly world-class example of its breed when it finally takes to the air in a couple of years time. In fact, you can check out the latest issue of Warbird Digest (issue #76) for a full report on AirCorps Aviation’s most recently completed restoration, TFLM’s P-51C Mustang Lope’s Hope 3rd, complete with air-to-air photography… The Mustang is simply stunning!
Getting back the Thunderbolt… We recently received a restoration update on the project from Chuck Cravens, and thought you would like to see what the team at AirCorps has been up to these past few months!
October/November 2017 Texas Flying Legends Museum P-47 Update
By Chuck Cravens
In October and November, for the first time we began some assembly of major airframe components. Other work on the P-47 centered on parts fabrication, disassembling the vintage fuselage, beginning the new fuselage, and assembling the fixed tail surfaces.
Parts Fabrication
In a Thunderbolt, exhaust gas fumes in the ducts back to the turbo supercharger and fuel fumes in the high pressure induction duct running back to the engine can present a problem not common in other fighters. A great deal of engineering went into keeping those fumes where they belong and safely away from the pilot.
Fuselage Disassembly
The fuselage was further disassembled in order to use the parts as patterns as we begin assembling the new fuselage in the fixture. Parts that appeared usable were inspected. With the fuselage in sections, various parts and assemblies can be accessed easily while apart or the sections can be set back together for a more overall look.
Empennage
The vertical stabilizer skins were riveted on permanently this month. The horizontals skins have been permanently installed for a while now. Once both were skinned, they were assembled; the first, large, identifiable Thunderbolt parts to go together on the project!
Assembled Horizontal and Vertical Stabilizers
It is always great to see major, identifiable airplane components come together as a project progresses. This time we have the tail surfaces joined together.
And that’s all for this month. WarbirdsNews wishes to thank AirCorps Aviation, Chuck Cravens (for the words) and John LaTourelle (for the images) for making this report possible! We look forwards to bringing more restoration reports on progress with this rare machine in the coming months.
Related Articles
Texas Flying Legends Museum’s P-51C Mustang ‘Lopes Hope 3rd’ Flies!
Texas Flying Legends’ Razorback P-47D – A History
Texas Flying Legends P-51C – Restoration Report – June/July 2017
Finding Loren: The Life, Death and Discovery of a P-47…
AirCorps Aviation Launches Aeroscan, 3D Laser Scanning Technology
Cadet Air Corps Museum AT-10 Restoration Project
Richard Mallory Allnutt's aviation passion ignited at the 1974 Farnborough Airshow. Raised in 1970s Britain, he was immersed in WWII aviation lore. Moving to Washington DC, he frequented the Smithsonian’s National Air & Space Museum, meeting aviation legends.
After grad school, Richard worked for Lockheed-Martin but stayed devoted to aviation, volunteering at museums and honing his photography skills. In 2013, he became the founding editor of Warbirds News, now Vintage Aviation News. With around 800 articles written, he focuses on supporting grassroots aviation groups.
Richard values the connections made in the aviation community and is proud to help grow Vintage Aviation News.
Be the first to comment
Graphic Design, Branding and Aviation Art