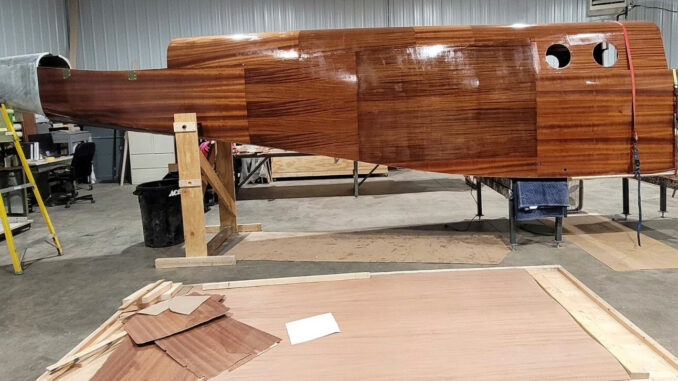
Periodically, we have presented reports from Chuck Cravens detailing the restoration of an ultra-rare Beechcraft AT-10 Wichita WWII advanced, multi-engine trainer, however, it has been more than a year since our last update. As mentioned in previous articles, the project belongs to the Cadet Air Corps Museum and comprises the remains of several airframes, but is primarily focused upon Wichita 41-27322. The restoration is taking place at world-renowned AirCorps Aviation in Bemidji, Minnesota, and here is their latest update on progress with the Wichita as it stands presently….
Most of the recent work on the AT-10 has centered upon the empennage. Each component has been removed – one at a time – from the original structure so that the vertical stabilizer stays in alignment without requiring a fixture to be made. As each part is reinstalled, the alignment remains true for the next part to be removed for restoration.
Some fuselage work has also taken place – such as trial-fitting the tail gear, tail cone, and the skin under the horizontal stabilizer.
The restoration team also applied a second coat of varnish to various wooden parts, the fuselage assembly, and the cockpit floor.
Empennage:
As Aaron inspected the project’s original empennage, it became clear that the vast majority of its glued joints would require separation and re-glueing. Thankfully, much of the wood comprising the inner structure was in good condition. As a result, Aaron was able to employ a procedure for restoring the vertical stabilizer which kept everything in alignment without any need for a fixture. He performed this task by removing only one rib assembly at a time for refurbishment. Separating this component into its component parts, he then stripped off any remaining old glue. After verifying each part’s airworthiness (fabricating replacements where necessary), he then glued the rib assembly back together and reinstalled the fully-refurbished component back where it belonged. Only two vertical stabilizer ribs required refabrication. By pursuing this process just one rib at a time, the remaining structure maintained its alignment perfectly.
Fuselage:
This cockpit section is currently at the paint shop where the black areas of the dash and the instrument and auxiliary panels will be painted.
Nacelle Components:
The project has several landing gear mounts available to choose from; after each is inspected, the best pair will undergo refurbishing to become part of the restored AT-10.
Want to get involved?
AirCorps Aviation is constantly looking for new technical material related to the AT-10. Due to the rarity of this aircraft, and the relatively low number produced, acquiring engineering drawings, parts catalogs, maintenance manuals, and other documentation has been much more difficult than with our past restorations. If you have any AT-10 material or know someone who does, the team would love to hear from you!
Be a part of helping the AT-10 return to the skies! Contact Ester Aube, by email or phone [email protected] or 218-444-4478
Furthermore, should anyone wish to contribute to the Cadet Air Corps Museum’s efforts, please contact board members:
Brooks Hurst: phone: +1 816 244 6927, e-mail: [email protected] Todd Graves: e-mail: [email protected]
Contributions are tax-deductible.
And that’s all for this edition of the AT-10 Restoration Report. Many thanks to Chuck Cravens and AirCorps Aviation for this article.
Related Articles
Cadet Air Corps Museum AT-10 Restoration – Fall 2023 Report
Cadet Air Corps Museum AT-10 Restoration – Spring 2021 Report
Cadet Air Corps Museum AT-10 Restoration – Summer 2020 Report
Cadet Air Corps Museum AT-10 Restoration – Fall 2018 Report
Cadet Air Corps Museum AT-10 Restoration – Summer 2018
Cadet Air Corps Museum’s Beechcraft AT-10 Wichita – Feb/Mar 2018…
Richard Mallory Allnutt's aviation passion ignited at the 1974 Farnborough Airshow. Raised in 1970s Britain, he was immersed in WWII aviation lore. Moving to Washington DC, he frequented the Smithsonian’s National Air & Space Museum, meeting aviation legends.
After grad school, Richard worked for Lockheed-Martin but stayed devoted to aviation, volunteering at museums and honing his photography skills. In 2013, he became the founding editor of Warbirds News, now Vintage Aviation News. With around 800 articles written, he focuses on supporting grassroots aviation groups.
Richard values the connections made in the aviation community and is proud to help grow Vintage Aviation News.
Be the first to comment
Graphic Design, Branding and Aviation Art