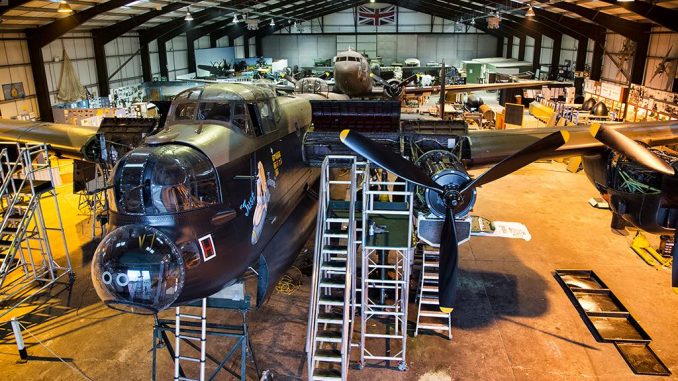
As regular readers will know, Avro Lancaster B.VII NX611 Just Jane is under restoration to airworthy condition with the Lincolnshire Aviation Heritage Centre at the former RAF East Kirkby airfield in Lincolnshire, England. The group continues to make magnificent progress, and we thought that everyone might like to see a recent (edited) report, reproduced here with permission.
You too can help support this important project; further details are HERE.
The Rivet Club – Newsletter 221
by Andrew Panton
Another busy month has passed, with some great visual progress! Volunteer Jacob has been busy progressing the static wingtip which is forming part of his structures training. We received the wooden bow for the wingtip last week and Jacob has drilled it to fit the ribs in the wingtip and trial-fitted it ready for the holes to be transferred from the skin. Once those holes are transferred, they then need to be countersunk and the whole bow varnished.
Dave M has completed the bench work on the former 38 for the rear fuselage of NX611 and it is ready to pin in place in the fuselage. Norm has been progressing the stringer work and with former 35 and 38 back in the fuselage he is able to finish the stringer work around those areas and trim the new stringers to the correct size. Once each stringer is set in place the cleats can then be riveted in place so it is ready to be finally fitted to the former. Cunningham Aero is working on the final pieces we are waiting on for the rear fuselage and they should be completed next week so we will be able to arrange shipping and then Phil can work on trimming them to fit the fuselage. With those pieces in place, we can then start fitting skins to the structure.
Andy D and Ade have been progressing with the FN5 front turret restoration and the FN82 tail turret systems work. Andy has been restoring the electrical power boxes that serve the rear turret ammunition booster feed motors. We don’t plan to have the motors serviceable but all of the parts of the system will be restored and look cosmetically correct. Ade has been starting to assemble all of the sub-assemblies that there are within the FN5 front turret. He started with the top hoop that holds the rotating service joint for the hydraulics and electrics situated at the top center of the turret and created the join between the solid aluminum back and the Perspex front of the cupola. The front turret restoration is awaiting some replacement rotating rings before the whole turret can be reassembled so working on subassemblies is allowing progress while we source the required rings.
NX611 is structurally complete now, it just requires the powerplant work to be completed. The closure and inspection panels have been fitted along with the port side valance and undercarriage door using hundreds of screws and bolts as well as some aching arms! NX664 donor rear-mid fuselage has also been making progress with further inspections showing problems with some of the repair work that was done to the fuselage prior to its arrival here. Some of the former repairs are not quite the correct shape as they do not meet the stringers and skins correctly. The only solution to this is to remake parts of the formers to the correct shape and create a repair. Dennis has been working on the rea-mid fuselage turret plug. The turret plug is a mod that was implemented for l’Aeronavale Lancasters as they removed the mid-upper turret and used this plug to fill the hole. Although we will not be using the plug while we fit the rear-mid fuselage section we will repair it ready for the French to fit it when they receive the rear-mid fuselage back after we have used it.
Our GoFundMe wings campaign has reached over £63,060 of the £500,000 required! Thank you to everyone who has contributed as you have helped us to pay for the jigs and aluminum. If you would like to contribute to the Wings Fund and receive your special Wings Fund badge then please click on the button below (badges are sent for donations above £50)
Many thanks for your support.
Andrew Panton
SUPPORT JUST JANE @ WINGS FUND
The latest restoration video…
That’s all for this particular update. We hope that you have enjoyed reading it. As can be seen, a lot of work remains to be done, but the aircraft is well on the way back to flying condition. It is being done in a methodical and careful manner in order to keep the aircraft available for ground-running operations during the summer months. For those interested in helping support this important project, please click HERE
Be sure to check out their store HERE as well… There are many cool items to buy that will help get Just Jane back in the air!
Related Articles
Lancaster NX611 ‘Just Jane’ – Restoration Update 201
Lancaster NX611 ‘Just Jane’ – Restoration Update 185
Lancaster NX611 ‘Just Jane’ – Restoration Update 180
Bristol Bolingbroke Restoration Begins at Lincolnshire Aviation Heritage Centre
Lincolnshire Aviation Heritage Centre Adds a B-25J Mitchell
Lancaster NX611 ‘Just Jane’ – Restoration Update 174
Richard Mallory Allnutt's aviation passion ignited at the 1974 Farnborough Airshow. Raised in 1970s Britain, he was immersed in WWII aviation lore. Moving to Washington DC, he frequented the Smithsonian’s National Air & Space Museum, meeting aviation legends.
After grad school, Richard worked for Lockheed-Martin but stayed devoted to aviation, volunteering at museums and honing his photography skills. In 2013, he became the founding editor of Warbirds News, now Vintage Aviation News. With around 800 articles written, he focuses on supporting grassroots aviation groups.
Richard values the connections made in the aviation community and is proud to help grow Vintage Aviation News.
Please keep up the great work. In Windsor Ontario Canada, they are restoring a Lancaster, FM 212. Check out there Facebook page to see the progress. Giving a big shout out to the volunteers helping to restore these two birds.
Great stuff! Keep up the good work!
Fantastic to see! As an young lad in the 80’s i was lucky enough to have been allowed to look around NX611 while she was ‘gate guardian’ at RAF Scampton, i got to sit in all the crew positions and still have the photos, there can’t be many of my age that can say they’ve sat at the controls of a Lanc!!