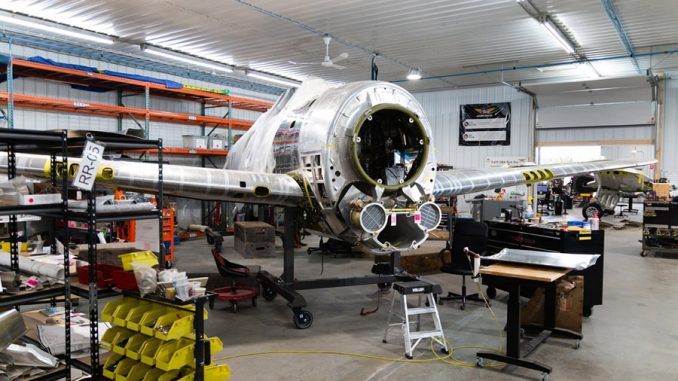
Warbird Digest has just received the May/June, 2021 report from Chuck Cravens concerning the restoration of the Dakota Territory Air Museum’s P-47D Thunderbolt 42-27609 at AirCorps Aviation in Bemidji, Minnesota. We thought our readers would be very interested to see how the project has progressed since our last article on this important project. So without further ado, here it goes!
Update
The oxygen tank installation and control surfaces for the wing and empennage were the focus of restoration work this month. The Thunderbolt is getting closer to the time that the R-2800 will be hung on the mounts.
Propeller Nut
Oxygen Tank Installation
The oxygen tanks were moved to a different location when the Christmas tree fuel tank was installed. Aaron has worked hard to duplicate this field modification.
Control Surfaces
The last major airframe assemblies, besides the engine installation, are the control surfaces. The flaps, ailerons, elevators, and rudder are all in progress.
Wheel Wells
Aaron completed much of the hydraulic plumbing and wiring in the main gear wheel wells this month.
Subcontractors
You probably noticed the Maytag and Kellett Aircraft Company logos on some of the previously pictured parts. These companies were important subcontractors on the P-47. While I have written a bit about subcontractors in previous updates, I think it is worth revisiting the subject.
Republic and each of the other major aircraft manufacturers depended upon subcontractors to support the massive production effort required during the war. Many subcontractors had produced consumer goods before the war but completely reworked their production lines to accommodate producing aircraft parts or assemblies.
“The air industry was called upon,” said the late Robert Gross, wartime President of Lockheed Aircraft Corp., “to build thousands of something it had built – only dozens of before. It was like a youth who is suddenly expected to go to college before he was graduated from primary school.” 1
To meet the unprecedented demand for high-volume production rates, aircraft companies had to subcontract the manufacture of as many assemblies as they could, often using companies with no prior involvement in aviation. The flexibility and willingness to make these drastic changes in support of the war effort was the essence of what came to be known as the Arsenal of Democracy.
“Nonaviation firms had to dismantle their plants and rebuild them for a vastly different type of work, they had to learn about tolerances undreamed of in their peacetime production, they had to retrain even their most skilled people.” 2
“The aviation firms, on the other hand, had to divert valuable management and engineering talent to the task of putting the licensees in business at a time when they could not spare a single worker from their own programs. They had to build the initial parts, components, and assemblies to provide the licensee with a “shakedown” assembly line. Pratt & Whitney, for instance, had to contribute 100 man-years of production and engineering talent to educate its licensees-Ford, Buick, Chevrolet, and Nash-Kelvinator-in the art of aircraft-engine production. The pressures were certainly not conducive to harmonious relations, yet the introduction of these new companies to aviation production was carried out with a minimum of friction.“ 3
1 Karl G. Harr, Jr., Industry and World War II,AIR FORCE I SPACE DIGEST • September 1965, p55
2 Karl G. Harr, Jr., Industry and World War II,AIR FORCE I SPACE DIGEST • September 1965, p58
3 Karl G. Harr, Jr., Industry and World War II,AIR FORCE I SPACE DIGEST • September 1965, p61
Kellett Autogyro Company designed and manufactured autogyro aircraft during the 1930’s and 40’s and helicopters from the late 1940’s through the 1950s. Because of its later involvement in helicopters, the Kellett Autogiro Company changed its name to the Kellett Aircraft Corporation in 1943 to reflect its broader array of products.
H. Wallace Kellett was president of Kellett Aircraft Company from its founding in 1929, but also performed the same role for the Republic Aviation Corporation beginning in 1939. He became Republic’s chairman of the board in 1943, remaining into 1945 when he resigned to again refocus on his own company.
While famous for their autogyros, a major proportion of Kellett’s production efforts during the war involved their subcontracting division. Kellett produced ailerons and flaps for the P-47, engine mounts for the B-24, flaps for the Martin Baltimore, stabilizers for the Curtiss Helldiver, welded parts for the Grumman Wildcat, flaps and other subassemblies for the P-40 and further items. 4
4 Howard Mingos, The 1944 Aircraft Yearbook, Official Publication of the Aeronautical Chamber of Commerce of America, Lancair Publications, New York, New York.
But Maytag and Kellett were just two of many P-47 subcontractors. The list below reveals some of the more important subcontractors for Republic’s Evansville Indiana plant and what they produced for the Thunderbolt.
- Firestone Tire & Rubber: self sealing fuel tanks, tires, engine oil seal “o” rings
- Servel Corporation: (manufacturer of heating and cooling appliances): almost all P-47 wings for the Evansville plant
- Hoosier Cardinal (an Evansville stamping company which made metal refrigerator parts, including ice cube trays, and lamps): tail surface sections
- Curtiss Electric: propellers
- General Electric: Turbosupercharger
- Pratt & Whitney: R-2800-59 engine
And that’s all for this month. We wish to thank AirCorps Aviation, Chuck Cravens for making this report possible! We look forwards to bringing more restoration reports on progress with this rare machine in the coming months. Be safe, and be well
Related Articles
Dakota Territory Air Museum’s P-47 Update – April/May, 2021
Dakota Territory Air Museum’s P-47 Update – March/April, 2021
Dakota Territory Air Museum’s P-47 Update – February, 2021
Dakota Territory Air Museum’s P-47 Update – January, 2021
Dakota Territory Air Museum’s P-47 Update – December, 2020
Dakota Territory Air Museum’s P-47 Update – November, 2020
Richard Mallory Allnutt's aviation passion ignited at the 1974 Farnborough Airshow. Raised in 1970s Britain, he was immersed in WWII aviation lore. Moving to Washington DC, he frequented the Smithsonian’s National Air & Space Museum, meeting aviation legends.
After grad school, Richard worked for Lockheed-Martin but stayed devoted to aviation, volunteering at museums and honing his photography skills. In 2013, he became the founding editor of Warbirds News, now Vintage Aviation News. With around 800 articles written, he focuses on supporting grassroots aviation groups.
Richard values the connections made in the aviation community and is proud to help grow Vintage Aviation News.
Be the first to comment
Graphic Design, Branding and Aviation Art