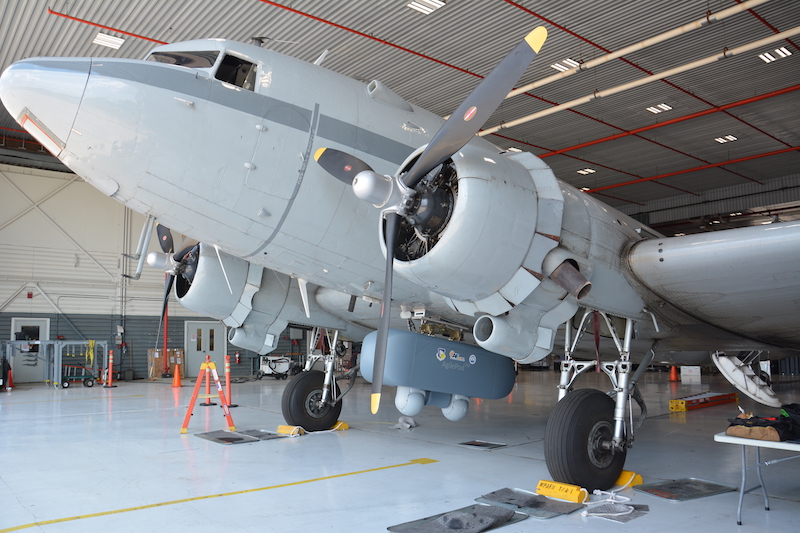
As most WarbirdsNews readers are well aware, the Douglas DC-3, along with its more prolific military variants, is an extraordinarily capable aircraft. Adapted from the Douglas Sleeper Transport, or DST, Donald Douglas could never have imagined how important his design would eventually be. It was the very first airliner to allow passenger service which didn’t depend upon air mail contracts to be profitable. And so many remained in service in the decades following its introduction, that it wasn’t until the 1970s when another airliner, the Boeing 727, became more numerous in global airline use.
The type is inexpensive, to operate, and offers a remarkably robust airframe capable of adapting to many uses, whether it be serving remote landing strips in the Antarctic on skis, flying freight and passengers in the Andes Mountains of South America, or dispersing oil spills in the North Sea with air-dropped detergent. This article features one particular example, now employed by the USAF Research Laboratory. AFRL is a global technical enterprise, leading the discovery, development, and integration of affordable warfighting technologies for our air, space, and cyberspace force. With a workforce of more than 10,000 across nine technical directorates and 40 other operations across the globe, the Air Force Research Laboratory provides a diverse portfolio of science and technology that range from fundamentally to advanced research and technology development.
A year of cutting-edge technology development and prototyping by Air Force Research Laboratory teams has culminated in a series of flight demonstrations as part of the Sensors Directorate Blue Guardian “Project Harvest Reaper.” AFRL’s AgilePod has embarked on a series of flight tests aboard a Douglas DC-3 aircraft in preparation for integration on the Air Force MQ-9 Reaper unmanned aerial vehicle later this year. The Lego-like pod is flying in multiple configurations with a mixture of sensor systems and technologies on board, with the goal to optimize the pod for operational activity and longevity.“AgilePod is a game-changer,” said Capt. Russell Shirey, Blue Guardian Program Manager at the AFRL Sensors Directorate. “This is a unique opportunity to highlight the benefits of modular open system architectures for airborne platforms.”
AgilePod, the first fully government-owned, multi-intelligence, reconfigurable pod, was developed using agile manufacturing technology and a modular open mission system approach to software design, resulting in a system capable of supporting rapid integration and mission agility to address emerging threats in new environments.The Blue Guardian team, in collaboration with the Manufacturing Technology Division of the Materials and Manufacturing Directorate and the Air Force Sensors Program Office, integrated Blue Guardian Open Adaptable Architecture into the AgilePod, culminating in a cross-directorate technology push to the warfighter. Open Adaptable Architecture is constructed on the Air Force’s Open Mission System (OMS) common set of software standards, and takes advantage of Sensor Open System Architectures, which are industry electrical and mechanical standards, to enable mission system interoperability. “Common connections and standards allows a greater suite of sensors to be rapidly integrated on the pod, enabling new capabilities. Having standards helps ensure an operator can successfully command a sensor to turn on or off, left or right, similar to turning a key in the ignition in a car, without having the change the other aspects of the system,” said Luke Borntrager, Blue Guardian Lead Engineer.
Unique to the AgilePod is that it is flight line reconfigurable, enabling operators to meet a variety of mission demands with multiple sensors on a single platform. A mixture of different pod configurations, ranging from 28 to 60 inches in length, are being tested on the DC-3, enabling simultaneous testing of multiple sensors including high-definition video, radar, infrared sensors and more.“Current sensor capabilities on aircraft are built for specific mission tasks, such as close air support or targeting, using proprietary software and hardware. Open system architecture standards combined with a single AgilePod having ‘plug-and-play’ capabilities and configurations enables one pod to perform hundreds of different mission sets. This is key for cost savings and increased sustainability,” said Shirey.
A standard data link and command and control system enables multiple sensor data analysis and command and control, enhancing warfighter capability and situational awareness. Additionally, a simulated MQ-9 Ground Control Station inside of the DC-3 enables operators to test data links and fine tune them prior to operational deployment on the Reaper.“The ability to rapidly test multiple configurations on the DC-3 aircraft gives us a ‘Lab-In-The-Sky’ concept and allows our team to wring out any issues before we move forward to the unmanned MQ-9, where we will not have the luxury of engineers in the cockpit,” said Shirey. Though the pod is currently in flight demonstration and testing, engineers are already looking towards future capabilities when it transitions to the MQ-9 platform. Once transitioned, it will support operations by the Air Force Life Cycle Management Center, Air Combat Command, Air Force Special Operations Command and others.
The fact that the AgilePod is a government-owned system—meaning that the government fully owns the digital data underlying the manufacturing of the platform—also plays into OMS design as it will enable industry to invest money into improving Air Force capabilities by creating new sensors, with the knowledge that they will be compatible with current and future platforms. “This bends the cost curve for sensor capabilities, processing and integration,” said Shirey. “It also opens up greater opportunities to partner with industry developers to enable the best capabilities for Air Force operational platforms.”
Government-owned data rights also allow for requirements and technology transitions to be competed across vendors. In other words, if a new sensor capability is required, a wider range of vendors will have the data required to compete for the contract. “Industry will play a major role in the future success of AgilePod,” said Shirey. “Response has been great, as they like the idea that they have the opportunity to put their sensors on the MQ-9 and other platforms through the AgilePod in the future.”
“In a memo earlier this year, the Secretary of Defense challenged the acquisition community to rapidly innovate and leverage industry advancements to defeat the adversary. AgilePod allows us to team with industry to develop the best solutions,” said Mark DiPadua, the AgilePod team lead in AFRL’s Manufacturing and Industrial Technologies Division, Materials and Manufacturing Directorate.“Our goal is to ensure intelligence, surveillance and reconnaissance capabilities can be more affordable and operationally flexible for the warfighter,” said Shirey. “That’s what these demonstration flights will help us achieve as we head towards the future of ISR.”
—
The AFRL Blue Guardian program aims to research, develop and demonstrate advanced sensor and rapid integration technologies using open system architectures to bridge the gap between the laboratory and the warfighter. For the Harvest Reaper project, Blue Guardian is working with the AFRL Materials and Manufacturing Directorate’s AgilePod team to demonstrate the cost saving benefits of an open architecture, reconfigurable C4ISR pod system.
Over 60 years ago I took my first airplane trip in a NWA DC-3. It was to visit my intended bride whose father was a Captain with NWA based in MSP. If any one would like a picture of that proud bird which was later used as the “Eisenhower Special” during Ike’s Presidential Campaign’ let me know…..
This article is supposed to be about warbirds. The author put forth little effort. There were literally three sentences on the DC3. Who operates N92578? Who flies it? Who maintains it? What is its history? Did it serve in the war? Was it an airliner? Thats what I would like to read in warbird news. The article was previously written for the Air force and is posted on the Wright Patterson website. Poor job author!!
Darrin, I can understand your comments but our thought was to highlight the longevity of the airplane rather than writing an article about the specific DC-3. I know warbird enthusiasts want to know how many new rivets vs original rivets each airplane has, but in this case we decided to focus on the big picture. The press release was distributed to accredited media, such Warbrids News by The Defense Video & Imagery Distribution System (DVIDS). The press release is published on multiple DOD websites, we added our one intro. Thanks for your comments.
I have about 2,000 hours in the Air Force C-47, beginning in Australia in 1944, and ending in South Korea in 1952. N. H. Happel, USAF Col (ret). I have 7,707 flight hours and I believe this is the best aircraft for forgiving pilot mistakes.
I have about 2,000 hours as a pilot in the USAF C-47, beginning in Australia in 1944 and ending in Korea in 1952. I have 7,707 flight hours and believe it is the most forgiving aircraft I have ever flown. I retired after 30 years as an Air Force Pilot
I issued the Airworthiness Cert. for N92578.