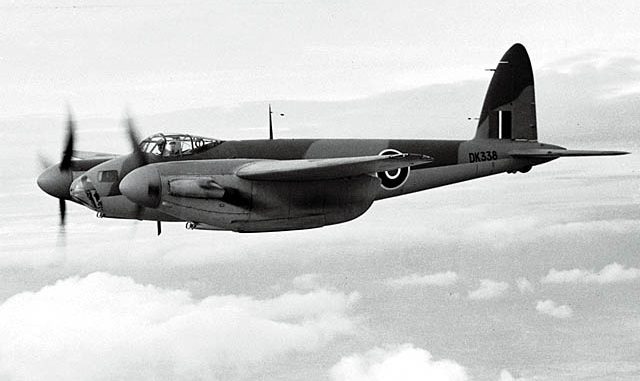
We have been following the efforts of the People’s Mosquito for some years now. The group has steadily made headway on their efforts to build an airworthy de Havilland Mosquito for Britain. This is a grass-roots effort, relying heavily upon small individual donations, as their name suggests. Even without the benefit a major financing source, they have been methodically working their way through the enormous technical and logistical issues in their endeavor, and have made remarkable progress. Working with Retrotec Ltd., the highly-experienced team with a proven track record of major restorations of both airframes and engines for museums and flying collections around the world. Retrotec has been hard at work recreating a set of fuselage moulds for the project. The following details, adapted from their recent press release, show where things stand at present…
Since the last update, Retrotec has begun engineering the ‘in-fills’ between the mould’s bulkheads. To form these parts, they needed an affordable material that was both efficient to shape and sufficiently sturdy. deHavilland originally used mahogany for this purpose, but this hardwood is not sustainable today sadly, and expensive. Thankfully, Retrotec found a ready substitute in Jelutong, a sustainable wood with the right material properties to sustain the significant pressures exerted during the moulding process. You will note in the photograph the trial fitting of two steel straps over the forward end of the mould; these will be used to apply pressure to the sandwich of plywood and balsa layers which will make up the fuselage.
As you can see from the main picture one of the moulds stands is now painted in bright RAF maintenance yellow. The mould in the picture is sitting in the new factory space which Retrotec is having constructed, a thoroughly ‘green’ facility which includes the latest insulation technology in the roof, and a method for collecting rainwater for use in the bathroom facilities.
To date, The People’s Mosquito (TPM) has invested just over £80,000 in the design and construction of the first Mosquito moulds in Britain for over 72 years. We are very close to completing them, both in financial and engineering terms, but we could really use your help in closing the gap – if you have a spare £1, please click on the donate button below.
How else you can help? Become a TPM Club Member, buy some merchandise, run a fundraiser or make a direct donation with gift aid or volunteer to help with our fundraising. In our next issue of this newsletter, we will be announcing how you can support more and find yourself associated for life with this historic part of Mosquito engineering!
Lloyd’s father, Royden Matthews, served with the RAF in Burma, India and Singapore. The Mosquito’s deployed here came into Royden’s RAF maintenance unit for repairs, typically as a result of enemy action, and particularly from ground fire. Lloyd explained that his Father was under orders not to photograph the Mossie lest the Japanese got hold of the images!
The lovely donation of these well travelled tools with a great Mosquito connection was certainly appreciated! We will be displaying them at our air show events this year, add a human story to the effort behind the project.
What have you got in your attic, garage or shed? We would love to hear from you! Please contact us if you can HERE.
Related Articles
The People’s Mosquito – Fuselage Molds Begin to Take Shape
People’s Mosquito Contracts with Retrotec to Deliver UK-built Flying Mosquito
The People’s Mosquito – Project Update – February, 2018
de Havilland Mosquito – Trans-Atlantic Collaboration Helps Unlock Her Secrets
Massive Cache of deHavilland Mosquito Plans Discovered
People’s Mosquito – Restoration Update
Richard Mallory Allnutt's aviation passion ignited at the 1974 Farnborough Airshow. Raised in 1970s Britain, he was immersed in WWII aviation lore. Moving to Washington DC, he frequented the Smithsonian’s National Air & Space Museum, meeting aviation legends.
After grad school, Richard worked for Lockheed-Martin but stayed devoted to aviation, volunteering at museums and honing his photography skills. In 2013, he became the founding editor of Warbirds News, now Vintage Aviation News. With around 800 articles written, he focuses on supporting grassroots aviation groups.
Richard values the connections made in the aviation community and is proud to help grow Vintage Aviation News.
Be the first to comment
Graphic Design, Branding and Aviation Art